Zinc has a long and well-developed history as a building material. For more than 200 years it has been used to clad and roof buildings in Europe. During the last several decades, it has gained popularity on North American buildings for its sustainability, resiliency, recyclability and versatility. The benefits of architectural zinc products support criteria for several state and federal green building initiatives, and programs including BREEAM® certification, the Cradle to Cradle Products Innovation Institute, the Green Globes system and the U.S. Green Building Council’s LEED® rating system.
Architectural zinc façade and wall cladding systems are consistently chosen as an environmentally responsible, durable alternative to other exterior siding and panel materials. Zinc is efficient to produce and has almost no waste. In contrast to some synthetic materials used in façade applications, architectural grade zinc alloys contain none of the impurities that can leach heavy metals into the soil or release them into the atmosphere. Zinc is not combustible or harmed by UV rays; and it does not rot, rust or need repainting. Fabricated into wall cladding and façade systems, zinc requires no hazardous cleaning chemicals and little effort to maintain once it is installed on the facade.
Longevity is another of the key values that zinc offers. Used in façade and wall cladding systems, architectural zinc is capable of maintaining its self-healing, low-maintenance, corrosion-resistant performance with a potential lifespan of 100 years or more. At the end of the zinc product’s useful life on a building, the material remains 100% recyclable; without the loss of existing properties.
A proven and dependable material, architectural rolled zinc products complement both contemporary and traditional architectural styles, and fosters a connection to the natural environment. As buildings weather and age, their zinc façade products develop a recognizable patina unique to the projects’ sites. The patination process forms through exposure to the local climate to protect the zinc from corrosion and to continuously evolve as a natural metal artwork.
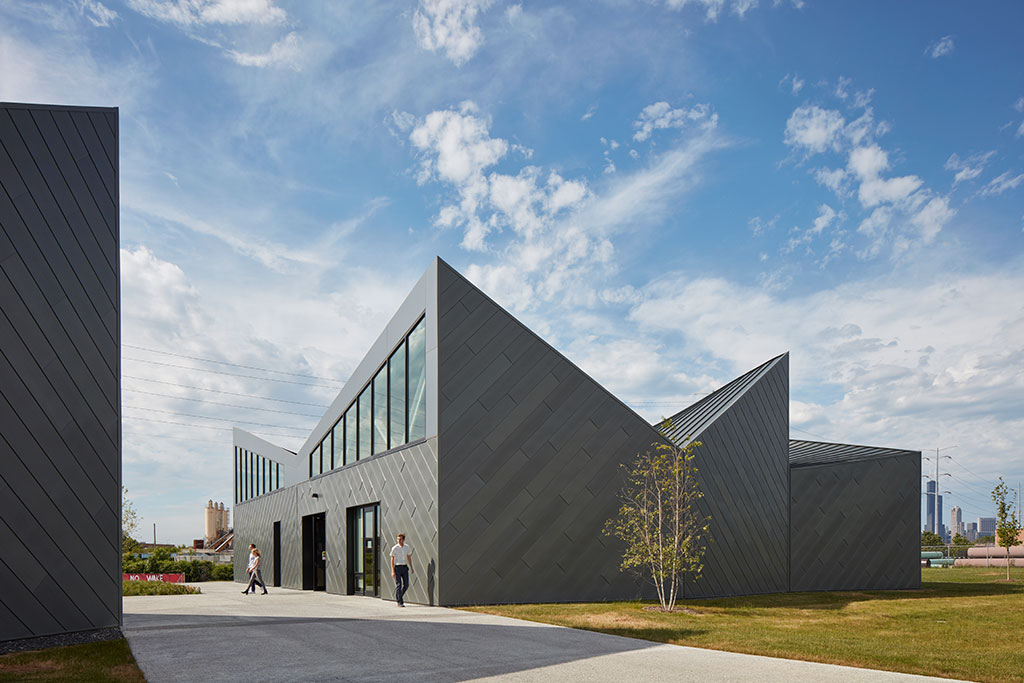
Eleanor Boathouse, Chicago, Illinois. Photo by Tom Harris, courtesy of Studio Gang and RHEINZINK
Systems, sizes and types
Zinc façade and wall cladding systems offer protections from weathering to the load-bearing, waterproof and insulating layers of the structure. Used in a rain screen assembly, zinc further protects the substrate and vapor barrier from weathering and allows the façade’s heat gain to dissipate through air convection. This strategy can be employed to help increase a building’s energy efficiency and reduce the heat island effect.
For façade systems, wall cladding products and other building applications, architectural zinc is manufactured in continuous 39.4- or 19.7-inch-wide strips. These are shipped as either flat sheets or rolled coils in 24, 22, 20, 18, 16 and 14-gauge thicknesses. Minimizing waste, these environmentally friendly and economical rolls generally yield two panels at 15.75- to 16.75-inch widths, depending on the profile. Tiles and panels can be fabricated as roll-formed or brake-formed engineered wall cladding systems. Any scrap that is generated is 100% recyclable.
Dimensions, system orientation, shapes, sizes and perforations can be further defined and customized to meet a project’s unique goals. Typical zinc façade cladding product examples include:
Example of façade wall tiles. Photo courtesy of RHEINZINK
Flat-lock tiles can be installed horizontally, vertically or diagonally with overlapping seams for a running bond or complex designs on flat or curved surfaces. Usual dimensions show face heights of 8 to16 inches or larger, with lengths spanning up to 10 feet. Larger sizes require a heavier gauge. Shapes vary from rectangular, square or diamond.
- Standing seam panels can be oriented horizontally, vertically and diagonally to produce the desired linear look. Standard seam heights are typically 1 and 1.5 inches. Lengths vary up to 40 feet with typical widths range from 12 to 16.75 inches.
- Horizontal panels allow for an emphasis on the reveal with face heights up to 10 inches and lengths up to 10 feet. Joint widths from zero to 1 inch are possible. A hairline joint minimizes shadow lines for a flush look. Panels and joints can be configured to create vertical joints or can be staggered with backer plates.
- Vertical reveal panels are similar to those offered for horizontal installations and feature face widths up to 13 inches. Vertical and horizontal panels can be combined to form innovative façade designs.
- Corrugated profiles are available as sinusoidal profiles or as trapezoidal, “box” profiles to clad large areas with ease using either exposed or concealed fasteners. Panels can be installed horizontally, vertically or diagonally. Common sinusoidal profiles have heights of 0.5 and 0.875 inches. The typical sine frequency is 2.67 inches. Trapezoidal profiles for wall applications often present a strong shadow effect with depths up to 2 inches.
- Cassette panels are often a part of an engineered curtain wall system. These panels allow for larger format panels through the use of reinforcements behind the panels and incorporated into the frames. For these large panels,16 gauge is typically recommended.
- Perforated panels provide the benefits of zinc, combined with advantages of daylighting and passive solar shading, plus low-maintenance punched openings that naturally patina.
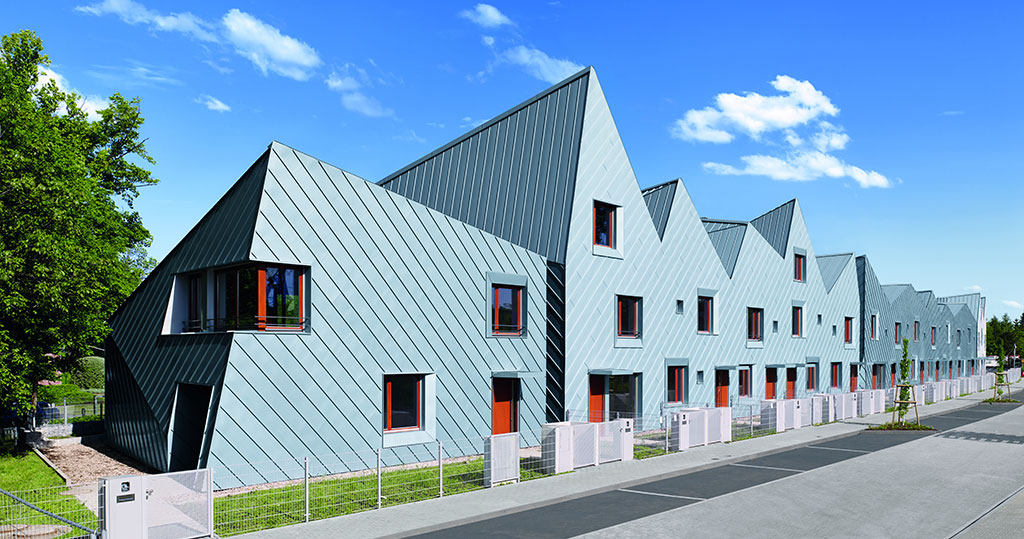
Example of standing seam panels. Photo courtesy of RHEINZINK
Patination and coloration
Mill-finish zinc starts with a bright surface similar to raw aluminum. Most architects, however, select zinc for its future patina appearance. Like copper, zinc develops its distinctive patina, or surface crust, based on the alloy composition and local environmental conditions.
The patination of architectural zinc products forms through a two-step chemical reaction. The zinc combines with water and oxygen to form zinc hydroxide, and then with carbon dioxide in free-flowing air, the zinc generates a dense outer layer insoluble to water and a packed inner layer of alkaline zinc carbonate.
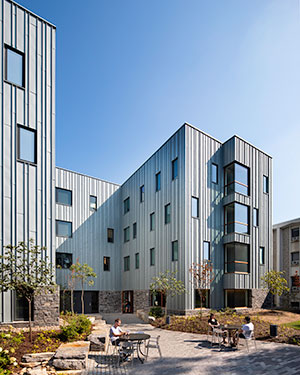
LEED Platinum, High Street Residence Hall at Dickinson College, Carlisle, Pennsylvania. Photo by Chris Cooper, courtesy of RHEINZINK
A patina’s formation is a process of the gradual growing together of zinc carbonate “freckles” and the rate of its formation is related to the slope of the surface. The patina will form slower on a vertical wall surface than on a slightly pitched roof. The patination speed can vary between six months and five years or more, depending on climatic conditions. The more exposure to wetting and drying cycles, the quicker the patina will develop. After the true patina has fully formed the process will slow down but never stops. Ultimately, the natural patina will form to a soft blue-gray or graphite-gray color, depending on the alloy.
While the basis of the patina is alkaline zinc carbonate, additional substances are incorporated from the local humidity, rainfall, snowfall and air pollution levels. This is why the color of the patina can vary from one place to another. The natural patina will appear lighter when used in marine locations where the air contains chlorides. When used in environments where sulfur levels are higher, the patina may appear somewhat darker. In marine environments, a blue-gray zinc frequently is selected for aesthetic reasons. The typical deposits of chlorides (salt) in marine environments are not as visible on blue-gray as the darker graphite-gray.
For projects requiring an initial or exact color, there are three common methods to adjust the zinc’s color prior to installation:
- Pickling is a pre-treatment process that chemically etches the metal and derives the color for the alloy. The resulting appearance brings out the metal’s natural gray color and subtle grain texture, and will naturally patinate as it ages.
- Phosphating is a treatment where phosphate crystals are deposited on the surface to create a darker color from the titanium or copper alloy. The resulting color is produced by the coating.
- Color coating is applied to the zinc and seals the metal with a selected color during its manufacturing process. The resulting color is imparted by the coating and no patina will form.
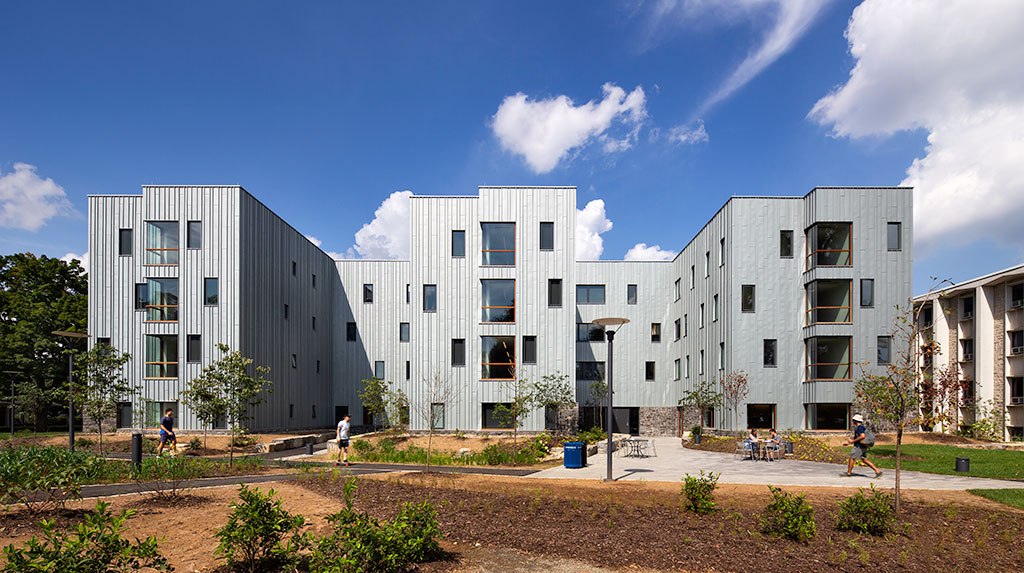
LEED Platinum, High Street Residence Hall at Dickinson College, Carlisle, Pennsylvania. Photo by Chris Cooper, courtesy of RHEINZINK
Composition and cost considerations
As a “green” material, zinc is efficient to produce due to its low melting point and it malleability to shape. Zinc slabs are formed by transferring the hot liquid zinc alloy from the induction furnace to the casting, where it is subjected to a carefully regulated pressure and cooling process. The resulting slabs are converted into either sheets or rolls of material.
It requires 25% to 33% less energy to produce than metals such as aluminum, copper and stainless steel. Using recycled zinc material requires 5% less energy than smelting raw material. Thoughtful manufacturers increase zinc’s efficient, environmental production by immediately returning any scrap to the production stream, utilizing state-of-the-art equipment to minimize emissions, and incorporating both pre- and post-consumer recycled content in the resulting material.
Architectural zinc material manufacturers use high-grade zinc with trace elements of titanium and copper. The metal alloy does not contain lead, iron, cadmium, selenium, manganese or magnesium, which have been associated with environmental and wellness concerns.
ASTM B69-16 “Standard Specification for Architectural Rolled Zinc” is the current industry standard. It details Type 1 and Type 2 architectural rolled zinc, where Type 2 has a higher copper composition and a graphite-gray patina.
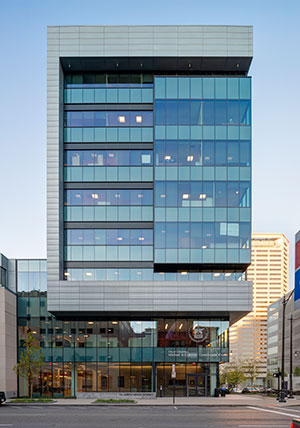
LEED Silver, Michael G. Coleman Center, Columbus, Ohio. Photo by Curt Clayton, Clayton Studio, courtesy of RHEINZINK
As part of the architectural building team, the specifier should qualify zinc manufacturers based on material quality, flatness, finish color, texture, selected panel profile, application system, availability, customer service and technical support. Selected zinc material manufacturers should provide product data, details and instructions, as well as material samples for submittal. These are accompanied by engineering calculations and shop drawings provided by the subcontractor. The calculations must be prepared and stamped by a professional structural engineer who is licensed and registered in the same location as the project.
Shop drawings typically include:
- Layouts of panels on all wall elevations
- Actual dimensions and seams
- Details of panel terminations, edge conditions, joints, corners, panel profiles, supports, attachments, trim, flashings, closures and special considerations.
To ensure the zinc façade system meets the project’s aesthetic and performance requirements, a mock-up may be necessary. This is produced using the specified materials and methods, and quality control standards. If needed, a full-size mock-up may be installed on location for a final approval.
Benefiting all involved on the project, most architectural zinc manufacturers offer in-depth information on efficient and cost-effective fabrication and installation. As examples:
- Roll-forming zinc panels are almost always less expensive than folding. Corrugated, standing seam and flush seam panels are all systems that can be roll-formed.
- If the material temperature is below 50 degrees Fahrenheit, zinc becomes brittle; the risk of fracture while folding increases as the temperature decreases.
- Zinc has a high coefficient of thermal expansion and should have accommodations in the design to allow for movement. Caulking often is not required at these critical junctures, helping to lower initial and lifetime costs, and to reduce recurring maintenance.
- The first consideration at any joint should be how to achieve the detail without solder or sealant. Sealants can limit airflow or trap moisture behind the zinc panels and decrease the panel’s lifespan. Beware that soldering at a high heat can burn through zinc. If soldering is essential, choose one that does not contain lead, cadmium or copper to maintain zinc’s environmental material attributes recognized by LEED and other green building programs.
- When detailing a zinc system, it should be noted that some details require less labor. Since labor represents 66% or more of the contract, expensive time-consuming details should be reviewed to ensure they are necessary to fulfill the architect’s vision.
- Panel sizes should be chosen to optimize the full width of the zinc sheet or coil and to minimize scrap material. Similarly, panel lengths should be limited for easier handling, fabricating and installing, as well as to reduce waste in the shop and the field.
- Fewer pieces can save time and labor. However, heavier gauge zinc or smaller panels may be necessary to reduce perceived waviness (oil-canning).
Selecting a zinc manufacturer that certifies its material to ASTM B69-16, and has demonstrated its experience in similar climates and applications, offers a good indication that they will prove successful on future projects. Designating one zinc manufacturer as the basis of design will further minimize opportunities variations in material performance.
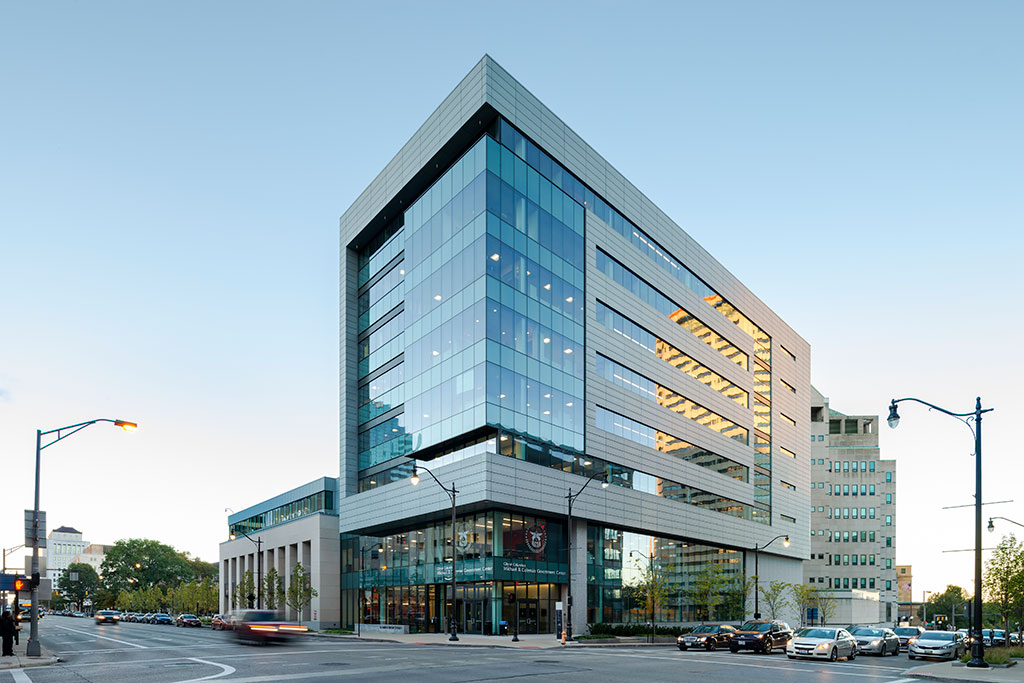
LEED Silver, Michael G. Coleman Center, Columbus, Ohio. Photo by Curt Clayton, Clayton Studio, courtesy of RHEINZINK
Compatibility, cleaning and longevity
Architectural rolled zinc is affected by its surrounding conditions. This means that wall cladding products loosely stacked on pallets or platforms must be protected by a weatherproof, ventilated covering. They cannot be stored in contact with other materials that could cause staining, denting or other surface damage.
Acidic materials are of key concern. Avoid placing zinc in contact with or downstream from acidic woods including oak, red cedar, white cedar, larch, hemlock or chestnut. Red rosin paper produces an acidic vapor and should never be used as a slip sheet. Use sealants that are PH-neutral.
Glass, aluminum, galvanized steel, stainless steel, painted steel and most solid, dry, building materials present no known compatibility issues with zinc. Corrosion to zinc is unusual, but can be caused by electrochemical reactions, such as when copper is installed above zinc. Chlorides also are problematic, and may be found as an additive in mortar or concrete as a bonding agent or to inhibit freezing. Contact with human perspiration should be avoided. Wearing clean gloves when handling and installing the zinc material may be necessary.
Zinc wall systems require minimal maintenance when exposed to normal weather and atmospheric conditions. Cleaning methods that use hazardous chemicals or remove the patina should be avoided. Clean, clear water; a soft sponge; and a non-acid based cleaner should take care of light dirt, dust, bird droppings. Wash in the same direction as the grain, then rinse thoroughly.
Always test a small area first to see if acceptable results are achieved. Check with the zinc manufacturer if more aggressive cleaning is needed to remove oily dirt, adhesive residue or heavy soiling. Pre-weathered zinc material also necessitates special considerations; if this surface is rubbed off or otherwise removed, the bright rolled material will appear. Consult with a zinc manufacturer for complete cleaning instructions.
Zinc is a “sacrificial” material. When it is scratched, scuffed or fingerprinted, the metal heals itself by re-patinating. With time and exposure to wetting and drying cycles, the former blemish will patinate and blend to match.
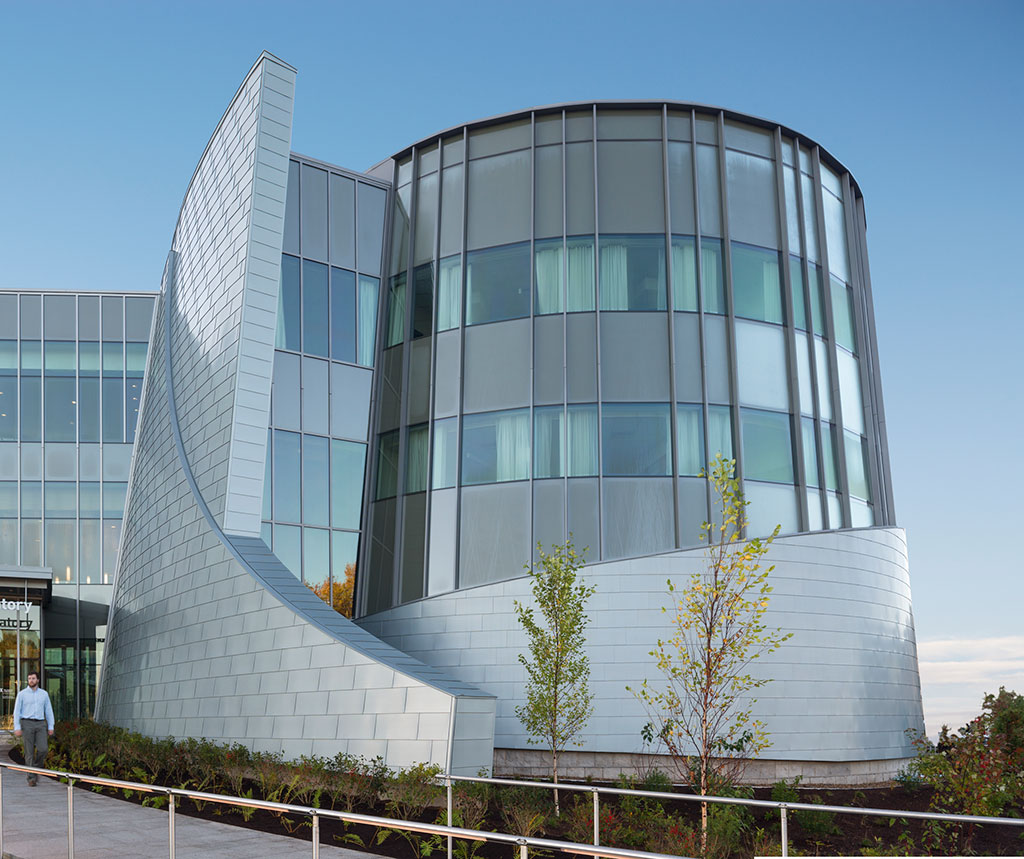
LEED Gold, Jackson Laboratory for Genomic Medicine, Farmington, Connecticut. Photo by Robert Benson Photography, courtesy of RHEINZINK
Architectural rolled zinc is largely considered a sustainable building material. Based on known ore reserves, the world’s zinc supply is estimated in excess of 200 million tons and expected to last approximately 700 years. Extending this timeframe, zinc is a 100%, infinitely recyclable material, and zinc scrap metal also eliminates waste and promotes re-use. More than 90% of zinc-containing products are recycled at the end of their useful life.
Consider the entire lifecycle of a product or material, the Cradle to Cradle Products Innovation Institute’s evaluation differs from other certifications in its focus on safe, sustainable products for a circular economy. To receive Cradle to Cradle certification, products are assessed from material generation until its re-use across five categories: material health, material reuse, renewable energy and carbon management, water stewardship, and social fairness.
Architectural zinc products that have earned Cradle to Cradle certification demonstrate their product’s material does not release any toxic substances during usage, deconstruction and recycling; that it retains its original properties without loss of performance, and that can be re-used as a new item of at least equal value. This is known as upcycling; whereas downcycling results in recycling material to become inferior products, and non-recyclable products will be sent to a landfill.
The analysis and transparency offered by Cradle to Cradle certifications and Environmental Product Declarations serve to inform design professionals in their material selection for sustainable building projects. Environmentally responsible zinc partners are generous in sharing their documentation and expertise, supporting the project from schematic design through construction, and backing their material with a warranty.
A coordinated effort between design, specification, fabrication, installation and manufacturing professionals, will ensure building projects benefit from the versatility, resiliency, sustainability and natural beauty of zinc façade and wall cladding products with a longevity that can last for generations.
About the author
Brian Harpring serves as a regional technical sales manager at RHEINZINK America, Inc., where he educates, motivates and inspires architects, contractors and building owners interested in creating sustainable projects with architectural zinc roofing, façade and wall cladding systems. He can be reached at brian.harpring@rheinzink.com.