Project Overview
The new 266,000-sq. ft. mission hall global health sciences building at the University of California, San Francisco, is a defining project for the growing Mission Bay campus. In an effort to create stronger links between academic disciplines and campus sectors, the new building was envisioned as a “gateway,” organized around a series of interior and exterior spaces that offer a flexible, changeable, and visible center for collaboration and campus access.
Design guidelines established by the owner informed the massing and basic organization of the building, calling for simple volumes, consistent building heights and a base, body, and parapet tripartite organization, explains Moses Vaughan, of WRNS Studio in San Francisco, the architect on the project. At first, his team wasn’t sure that precast concrete could address these design requirements.
“While we knew that unitized precast construction would help us achieve budgetary goals, we were concerned that a typical glass-fiber-reinforced concrete (GFRC) architectural expression would not allow of the unique and animated sculptural solution we sought,” he says. But by working closely with Walters & Wolf, the precaster on the project, the team was able to “optimize the architectural opportunities” while staying within the practical requirements of a unitized wall panel system.
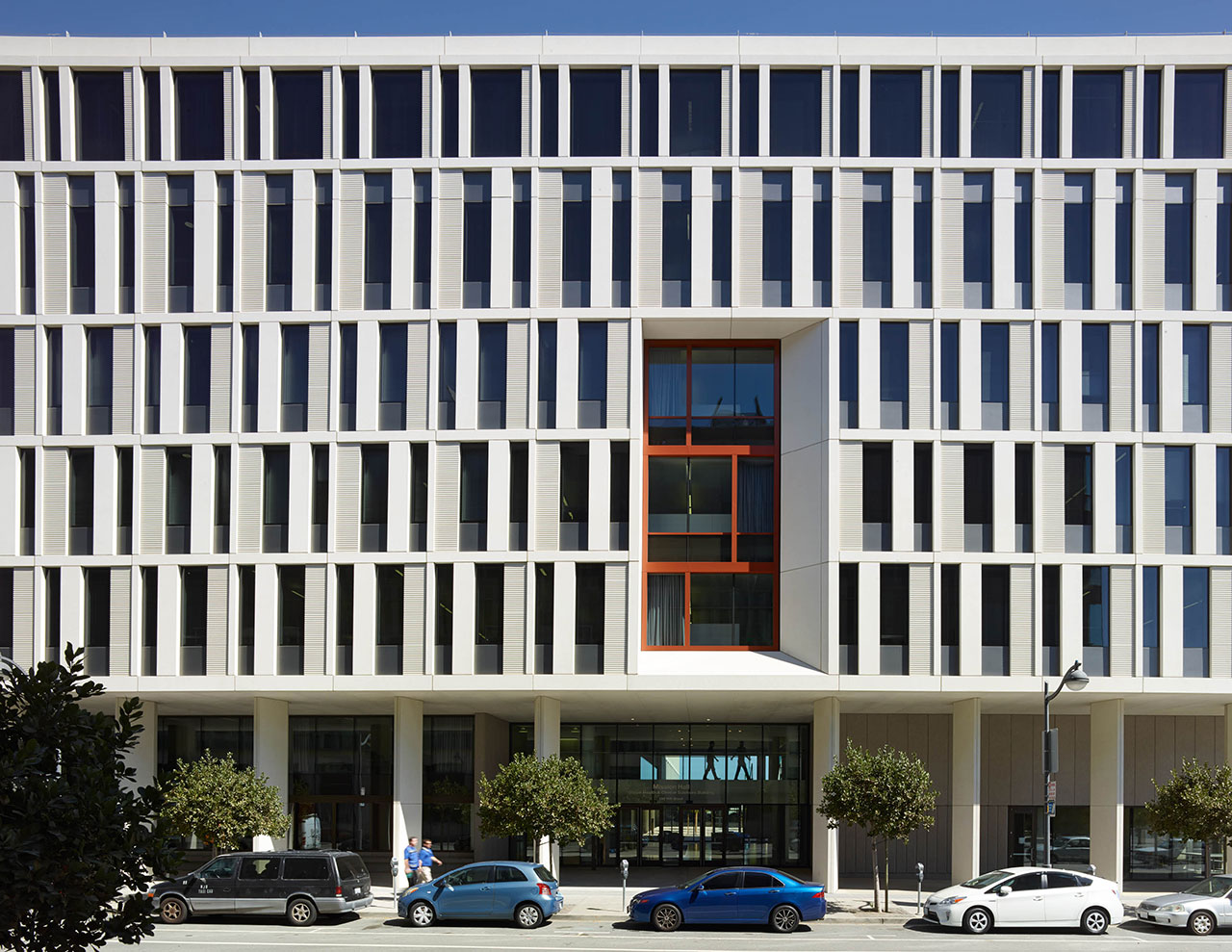
Photo credit: Bruce Damonte
The project also faced tight deadlines, and the owner expected a high-performing building that would stay watertight under a mid-level seismic event, explains Scott Campbell of Walters and Wolf. “This led to spirited debate between the teams on how best to solve this without compromising the building aesthetics,” he says.
In the end a variety of solutions were employed.
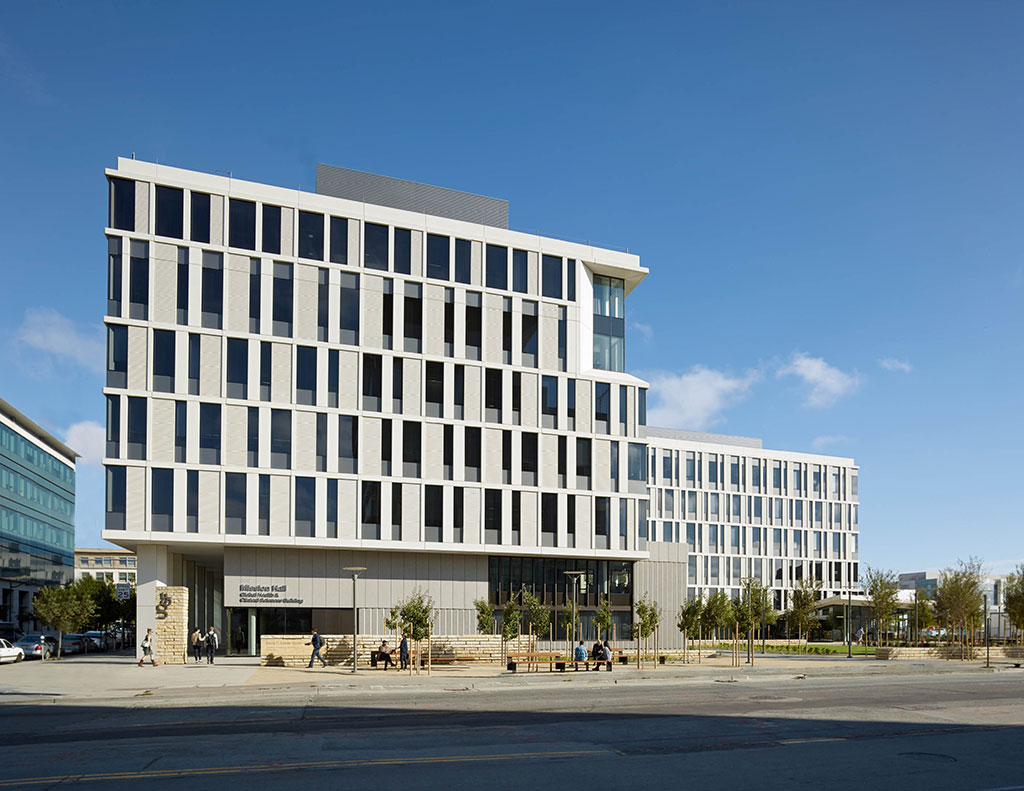
Photo credit: Bruce Damonte
Precast Solution
The building skin is comprised of GFRC units, vision glass, and metal spandrel panels on a panelized unit. “The GRFC appears as though it is a framework floating above the darker glass and metal elements underneath, creating the building’s outer mesh expression,” Vaughan says. The variability in the mesh is based on orientation and is realized by changing the amount of solid GFRC and vision glass within the panel. GFRC pilasters were presented in smooth and washboard-shadow, and the proportions of specific wall fragments and adjacent window-voids were adjusted for solar exposure, spatial and technical reasons, as well as façade-making. “The resulting panels vary between smooth and wash-board texture to provide shadow, scale, and variability,” he says. The color of the GFRC reflects the surrounding buildings on both the research and clinical side of the campus and offers a level of intricacy that allows the building to be enjoyed on multiple scales.
GRFC and precast concrete were also used throughout the building, including the base and upper floors, and in a uniquely designed “window box truss,” which allowed the glass to be contained entirely within the panel and thus installed at the precaster’s plant. “This made for a tremendous savings in the field schedule,” Campbell says.
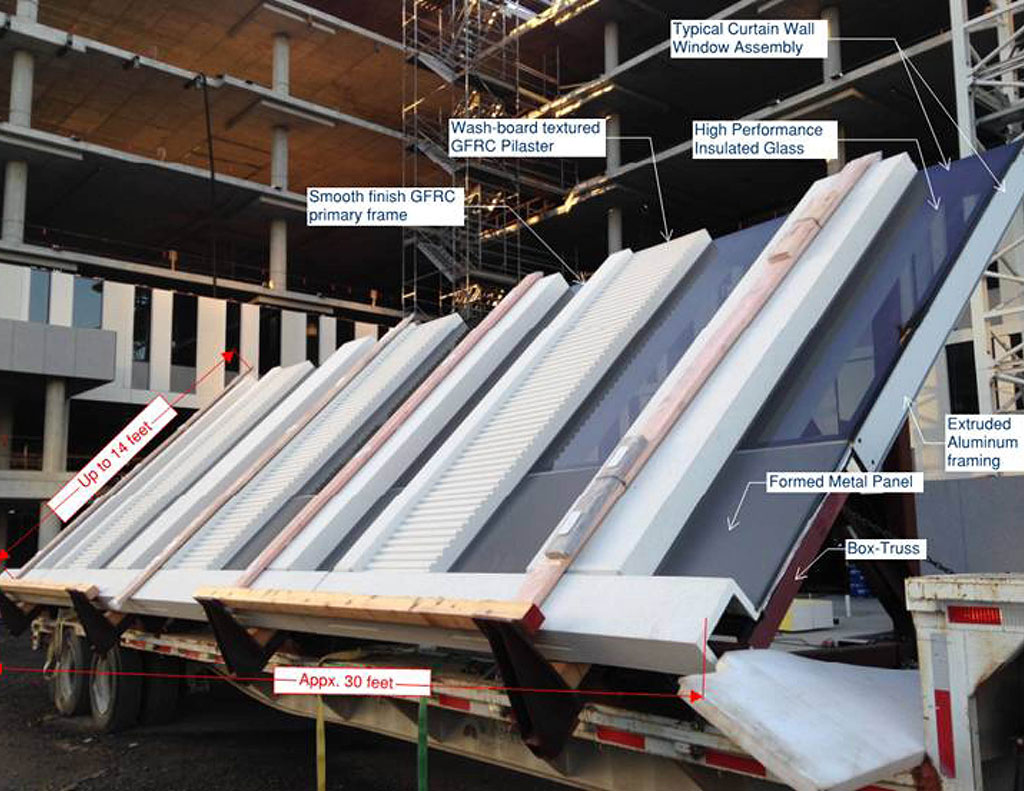
Photo credit: Bruce Damonte
“This project, and specifically the unitized GFRC building skin strategy, exemplifies the benefits of a successful lean construction approach,” Vaughan says. “All of the team members collaborated to bring added value to the project, balancing economy, aesthetics, performance, and sustainability.”
AWARDS
2016 Design Awards: Best Higher Education/University Building
PROJECT TEAM
Architect
WRNS Studio, San Francisco, Calif.
Engineer of Record
Rutherford & Chekene, San Francisco, Calif.
Contractor
Rudolph and Sletten, Redwood City, Calif.
Owner
UCSF Capital Programs & Facilities Management, San Francisco, Calif.
Precast Producer, PCI Certified Erector, and Precast Specialty Engineer
Walters & Wolf, Fremont, Calif.
Photo Credit
Bruce Damonte
KEY PROJECT ATTRIBUTES
• Innovative use of GFRC panels materials to achieve scale, texture, rhythm, and solar exposure goals.
• Panels were lightweight, cost effective, and more sustainable than cast-in-place concrete construction.
• Window box truss design encased glass entirely within the panel driving further time and cost savings.
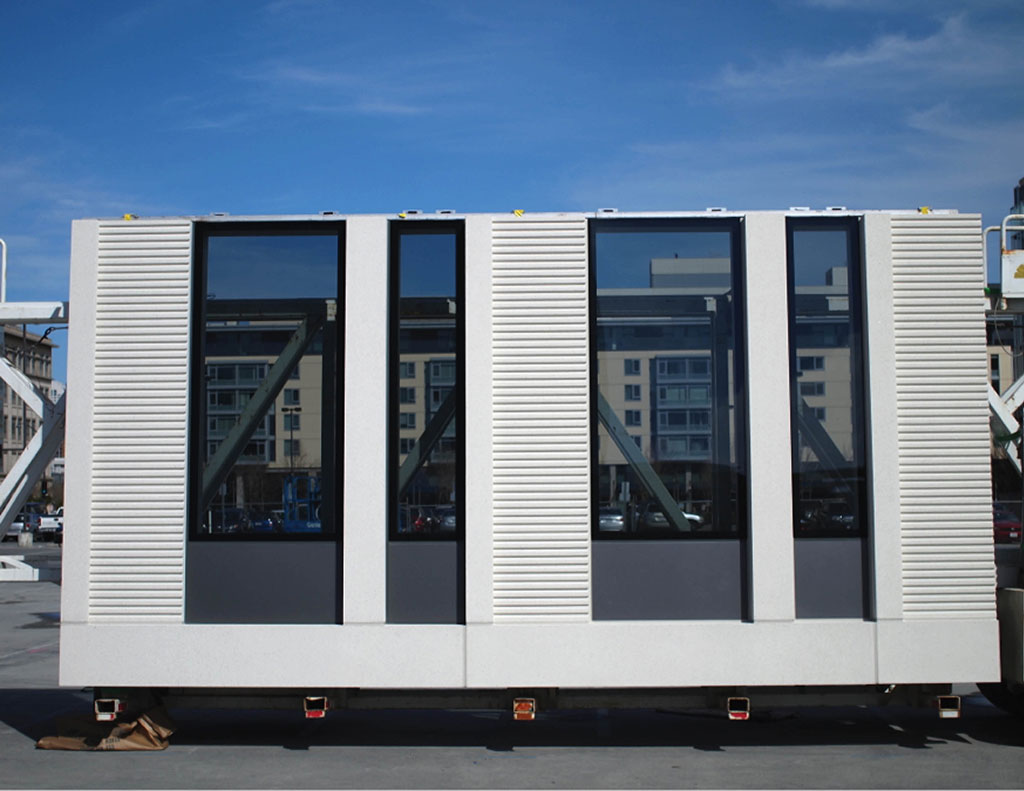
Photo credit: Bruce Damonte
PROJECT/PRECAST SCOPE
• Project Cost: $99,241,510
• Project Size: 266,000 sq. ft.
• Panelization featured a 30-ft-long truss to accommodate all four curtain wall versions.
• Erection of precast concrete elements was completed in less than a month.
• Precast concrete elements cost $4,200,000.
Editor’s Note: This article is was published by the Precast-Prestressed Concrete Institute (PCI), UCSF Mission Hall Global Health Sciences Building, and is being republished on PRISM with PCI’s permission. Please note this project won the 2016 PCI Design Award for the Best Higher Education/University Building. To find out more about the PCI Design Awards and other PCI awards programs, please visit the PCI awards programs page at https://www.pci.org/PCI/About/Awards/Awards_Programs.aspx.