Wind-driven facade systems add dynamic movement to building enclosures and wall systems. Responding to air currents, the flapper-panel design creates the look of rolling waves across the wall. These systems are suitable for both small- and large-scale projects. Popular applications include transit and parking facilities, cultural institutions, entertainment venues, and artistic installations.
Planning considerations
The first step in considering a successful kinetic façade installation is to understand the position of the structure relative to the surrounding environment. The local geography, jurisdictional requirements and building orientation will all be key contributors.
Property and setback limitations, as well as zoning and code considerations, need to be assessed. The appropriate cadastral map and relevant property documentation should be consulted to ensure that the façade’s flapper panels have enough clearance to exhibit a full range of motion without violating any setback requirements.
Some municipalities may require façade installations to comply with sign ordinances when lettering or designs are applied or expressed through the arrangement of multicolored flappers. Other jurisdictions may have restrictions on moving elements.
To ensure the wind-driven façade moves as intended, crucial considerations in the planning phase should include airflow, façade visibility, lighting, noise reduction and vandalism mitigation.
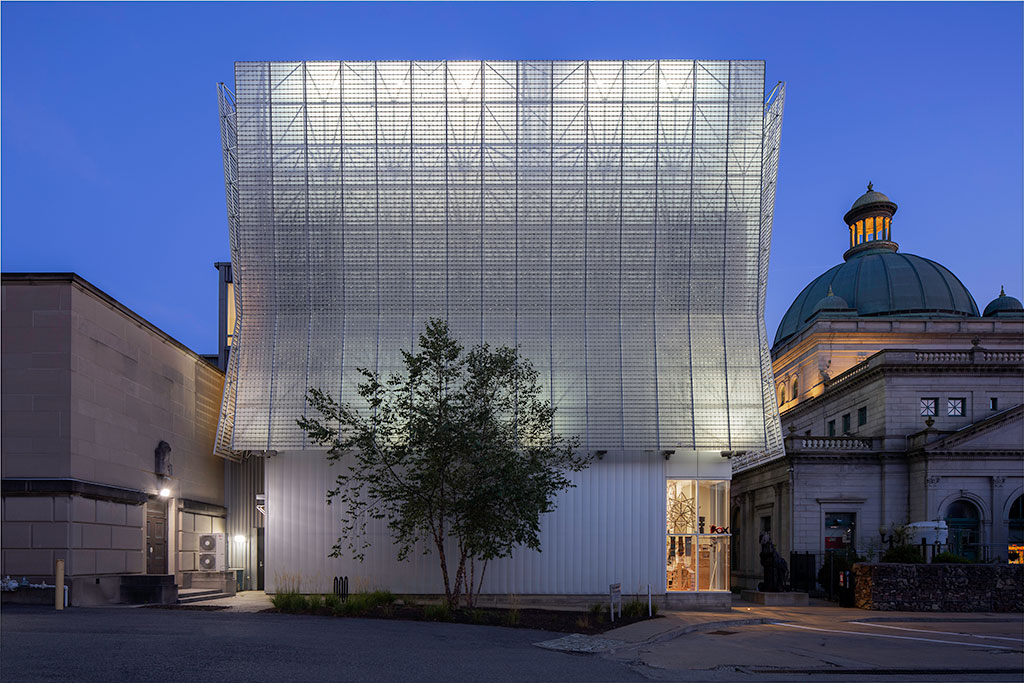
Pittsburgh Children’s Museum, Expansion & Remodel
Client: Children’s Museum of Pittsburgh
Artist: Ned Kahn
Architect: Koning Eizenberg
Pittsburgh Children’s Museum, Expansion & Remodel
Client: Children’s Museum of Pittsburgh
Artist: Ned Kahn
Architect: Koning Eizenberg
Façade manufacturer: EXTECH
Airflow
Kinetic facades can work with as little as 2 mph wind speeds depending on the flapper size, shape, configuration and material. Heavier material will be less responsive than lighter material.
Façade visibility
The viewing perspectives need to be considered to maximize visual impact of kinetic façade. In tight urban environments, where most vantage points are nearfield, smaller flapper elements should be considered to achieve a denser, less pixelated appearance. For installations where the façade likely will be viewed at greater distances, larger flapper sizes can be used to achieve the same visual impact at a lower cost. If the kinetic façade serves as a shading device, the aesthetic appearance of the system from within the building may need to be taken into account.
Lighting
The solar angles at which the sunlight strikes the façade’s elements can have a profound impact on the aesthetic. For specific environments, such as those near airports or in tight urban settings, glare resulting from the selection of highly reflective materials may be undesirable. In other cases, where indirect light is predominant, a material with more reflectance can accentuate the façade’s kinetic activity.
Noise reduction
All kinetic installations can produce some level of ambient sound under higher wind conditions. The suspension system, construction material and flapper geometry can be adjusted to ensure the level, tone and timbre of the resulting sound is acceptable. Many manufacturers engineer systems with spacers between the flappers to reduce the collateral noise. The volume and quality of sound generated by the installation should be considered as early as possible in the design and specification process, and verified with full-scale mockups.
Vandal mitigation
Like almost any reachable structural element of a building, a façade is vulnerable to vandalism and should be assessed to determine its susceptibility to such issues. Ground level elements should be given particular attention if they are within reach of pedestrians. In parking structures and other applications where façade elements are accessible, it may be worthwhile to install protective mesh on the rear of unitized sections to prevent malicious vandalism, or to apply anti-graffiti coatings on the flapper elements. In any case, the ease of flapper replacement should be considered in case damage may occur.
Performance considerations
Performance requirements are important on every building, and deserve extra attention with kinetic façade systems. Careful analysis is needed regarding the interaction between the kinetic façade elements and the building structure to which it is attached, as well as the impact of the structural behavior on the design and cost of the system.
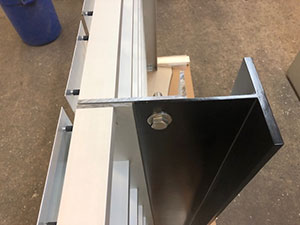
Photo courtesy of EXTECH
Structural loads, especially those due to positive and negative wind pressures, need to be assessed to ensure the façade system meets the required strength and the aesthetic requirements. Ice, snow and seismic loads may need to be reviewed in some applications.
The method of attaching the façade elements to the building needs to be examined and coordinated as early as possible during the design and specification phase. For example, will the kinetic panels be self-supporting, or will secondary supports need to be installed? In concrete structures, this means evaluating their embeds and anchors, their interaction with existing reinforcement configurations, and their required supporting system.
The kinetic façade system needs to be compatible with anticipated building movements. The attachment design should account for the dynamic deflections of various types of buildings and structural systems. In parking structures, for example, the dynamic deflections from vehicle traffic must be taken into account. Kinetic façade systems that cannot accommodate the required deflections run the risk of failure. It is, therefore, crucial that mounting systems are designed for these deflections to ensure long-term integrity of the system is maintained. Close coordination between the façade designer and manufacturer, and the engineer of record for the supporting building structure is critical even in the early phases of the design process.
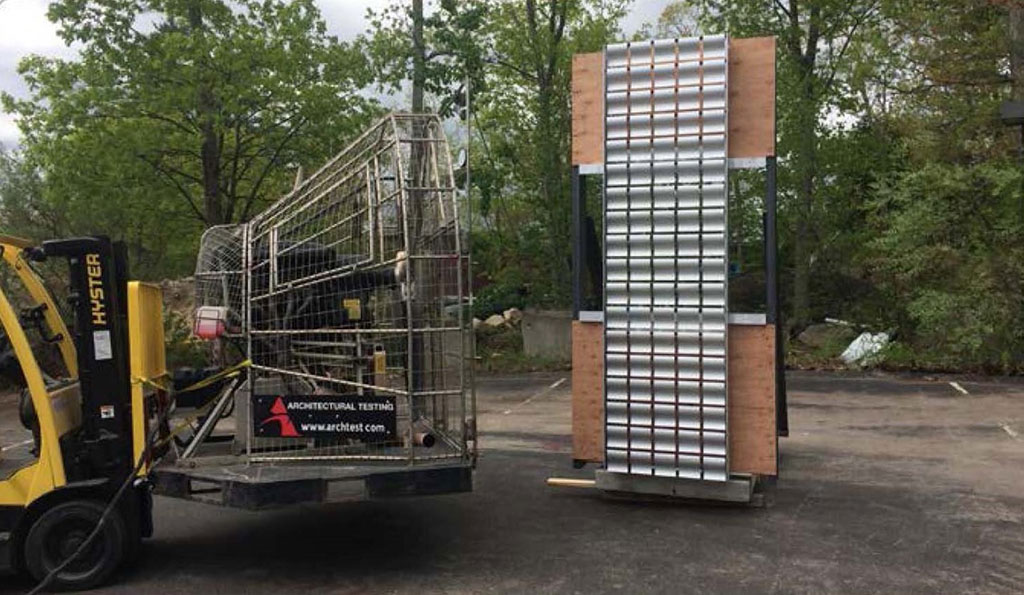
Photo courtesy of EXTECH
A building’s structural demands may govern the testing requirements of the kinetic façade, such as ASTM E-330/E-330M “Structural Performance of Exterior Windows, Doors, Skylights and Curtain Walls by Uniform Static Air Pressure Difference.” These testing requirements often are driven by local codes, however, the desired façade performance may be the determining factor.
Design and specification considerations
With a kinetic façade system, design and specification primarily focuses on material selection; the flapper elements’ size, shape, and spacing; and the suspension systems that support them. Integration of lighting elements also can affect the system’s final appearance.
Material selection
As with any façade, material selection and arrangement is critical to long-term performance of the system. Due to the dynamic nature of a kinetic façade, it is critical to incorporate movement and, therefore, to consider wear and proper selection of proven UV-resistant and abrasion-resistant materials. This often involves customized, accelerated testing of components and assemblies.
Physical mockups can assist the design team, building owner and sometimes, the jurisdictional authority in understanding the visual and auditory effects of the proposed façade.
Flapper and lighting elements
Wind-driven, dynamic façade systems support a wide variety of flapper shapes, sizes and materials. While aluminum is the most popular, other options include perforated materials, stainless steel, polycarbonate, polytetrafluoroethylene (PTFE), acrylic and even polyvinylidene fluoride (PVDF) films.
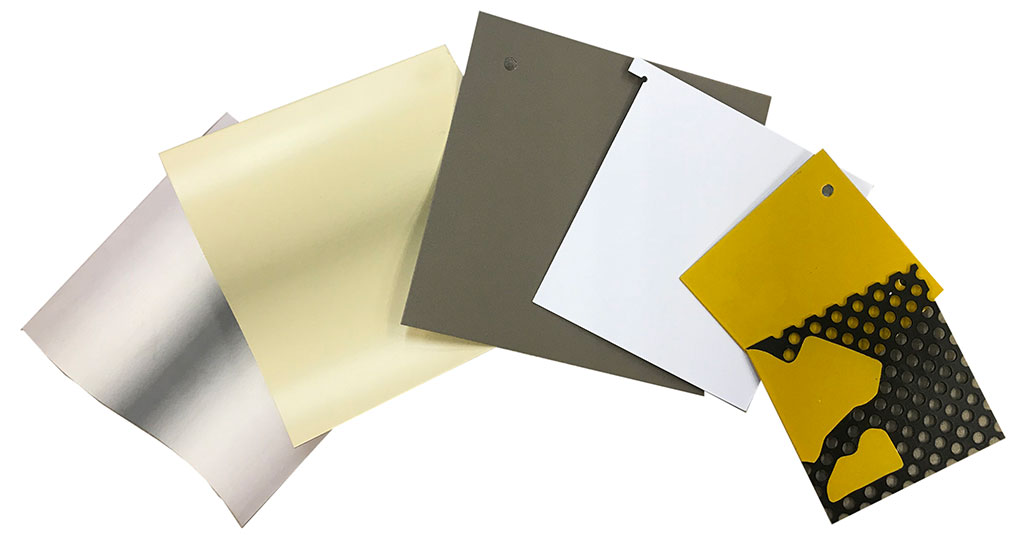
Photo courtesy of EXTECH
A wide variety of flapper finishes are available. Standard finishes include anodized aluminum or fluoropolymer paint. Higher gloss finishes, such as metallic coatings, tend to accentuate the visual kinetic action of the façade. Color-shifting and textured finishes produce interesting visual effects.
Patterns can be printed or perforated on flapper elements. This can range from basic screen printing of simple patterns, to full-color image printing. Large images can be segmented, or pixelated across the entire kinetic façade to bring a dynamic appearance to an artistic or branded image.
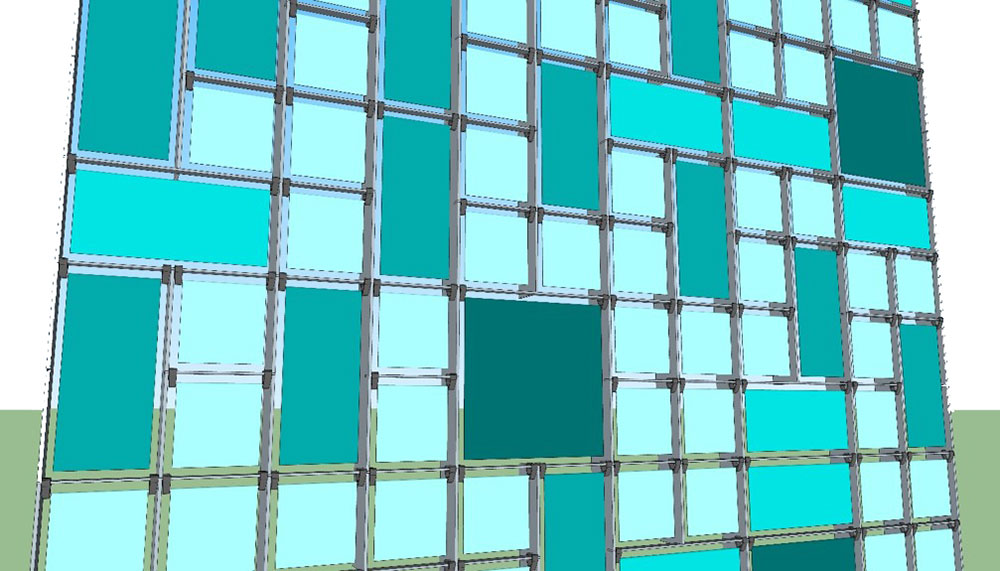
Photo courtesy of EXTECH
Flapper elements fabricated from translucent materials allow for natural light to pass through the façade. Translucent acrylic and polycarbonate materials can be specified with infrared-blocking coatings to help manage unwanted solar heat gain inside the building.
Anti-reflective coatings on polycarbonate materials can reduce glare during the day, and at night could act as a backdrop for projected images and lighting effects. Regardless of the flapper element’s material composition, many kinetic façade installations incorporate illumination during the evening. Face lighting from above can be used to emulate a daytime view, while dramatic effects can be achieved through the use of various night lighting including backlighting, uplighting, or wall wash lighting.
Suspension systems
To accommodate the specified flapper elements, there are three typical suspension systems to consider for wind-driven kinetic façade designs: rod-mount, pin-mount and drop-in. Each configuration possesses different performance and aesthetic characteristics and baseline costs. Modified and custom systems can be developed for unique project requirements.
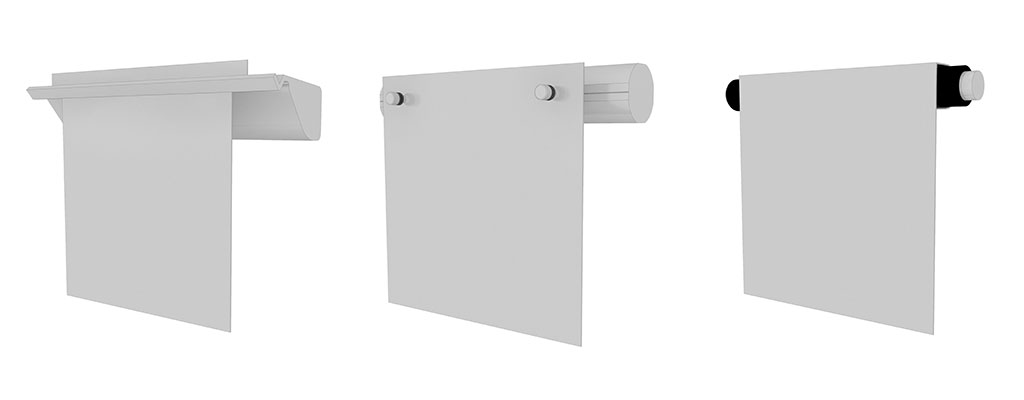
Suspension systems left to right: drop-in, pin-mount and rod-mount. Photos courtesy of EXTECH
For ease of delivery and installation, each of these motion systems usually is factory-unitized. Dimensions commonly range from 3 by 4 feet to 15 by 12 feet in vertical or horizontal orientations.
For optimal cost and performance value, the drop-in suspension system is recommended. In this configuration, T-shaped kinetic flappers are inserted into a specially designed “rung” extrusion system, significantly reducing the amount of time and labor required for fabrication.
The pin-mount suspension system lets the flapper elements seemingly float in front of the support rungs and side rails as a veil. This configuration minimizes the appearance of the supporting structure. The pin-mount system allows for mixing flapper shapes to create geometric patterns and for installation at various mounting points, facilitating changes in kinetic activity.
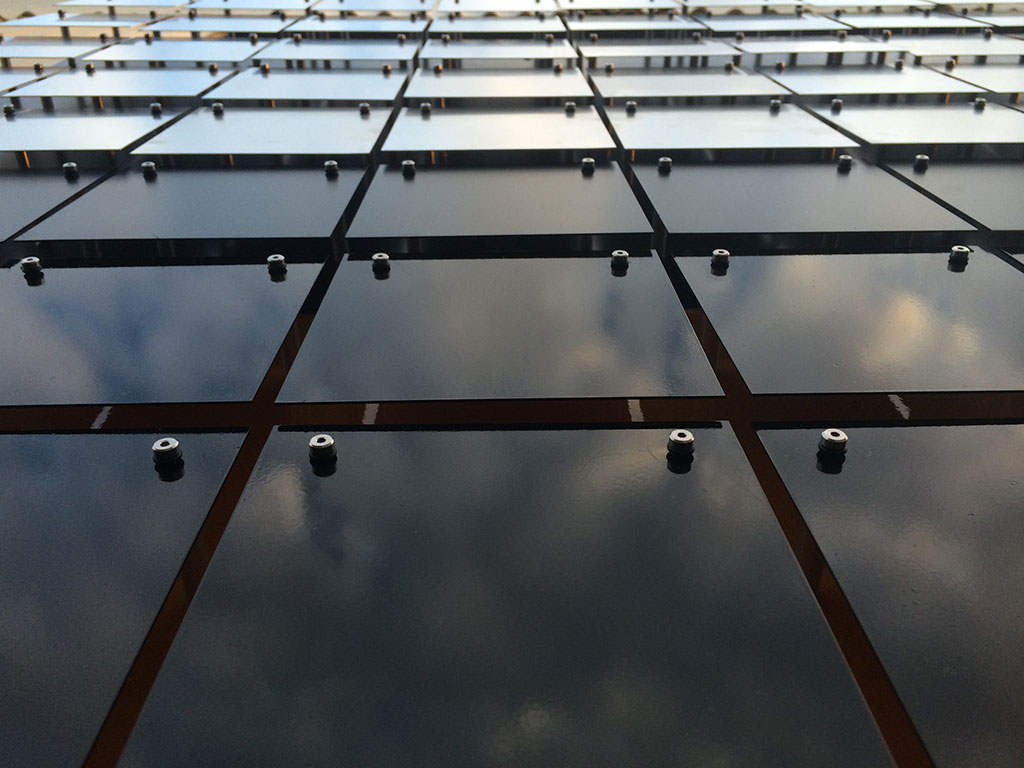
Pin-mount suspension system. Photo courtesy of EXTECH
Drop-in and pin-mount suspension systems allow the flappers to be removed and replaced without any specialized tools if repair or maintenance is needed. Both systems accommodate up to a 90-degree range of motion.
Offering a 360-degree range of motion for the individual flappers, the rod-mount suspension system allows for greater intermittent views through the kinetic façade and minimizes the appearance of the horizontal supporting structure from within the building. They can permit increased airflow and promote passive cooling. The vertical side rails are more prominent within the façade and the flappers can be replaced with simple tools.
Some manufacturers offer cable-mount suspension systems. These systems suspend the kinetic elements or flappers between a combination of horizontal and/or vertical cables. The flapper replacement for cable-mount systems can involve costly and time-consuming restringing or replacement of the entire cable section.
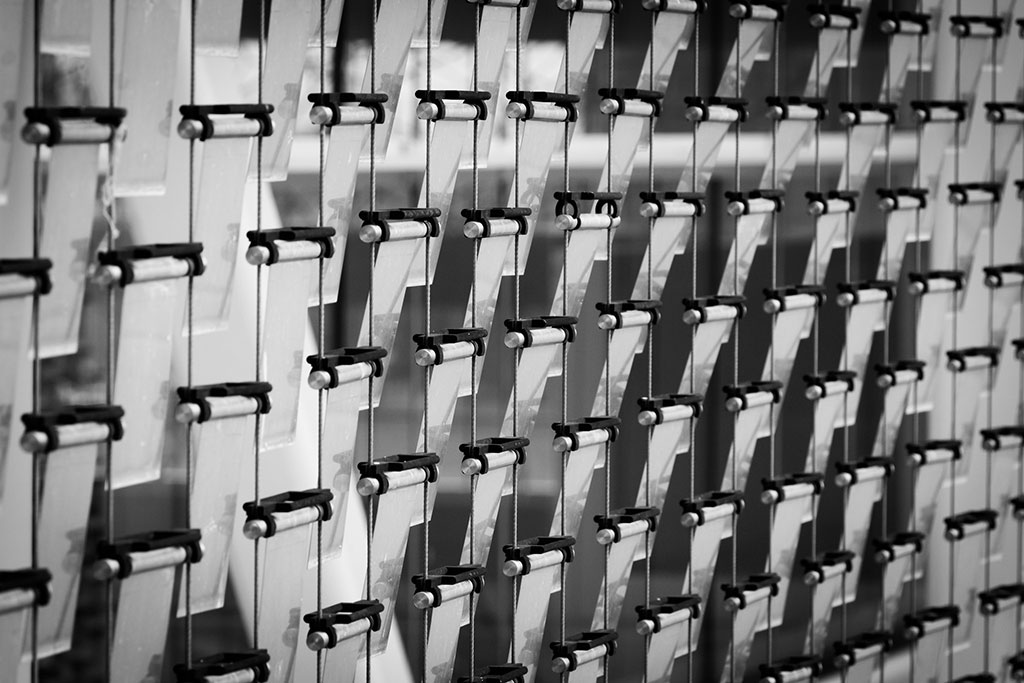
Cable-mount suspension system. Photos courtesy of EXTECH
Budget considerations
A project’s design and specification phase is the best opportunity to analyze aesthetic and performance requirements, and to make adjustments to ensure its success. Once the project moves into fabrication and installation, corrections become more costly.
Budgeting for a kinetic façade system entails striking a balance between the desired aesthetic and performance goals of the product. Since kinetic façade systems are delivered to a job site in pre-assembled units, most installations range from $9 to $15 per square foot depending on several factors plus labor costs.
Additional costs may be incurred as a result of testing requirements of the location or the application. Local labor costs, labor union requirements, site access, street closures, timing and scheduling, and project duration, are just some of the installation-related factors that can affect the final cost of kinetic façade systems.
In addition to the costs associated with installation, system type and testing, other relatively small hardware or structural changes can have a profound impact on the final cost. These include the following.
Flapper density
Flapper density is defined as the number of flappers per square foot. The smaller the flappers, the more individual handling, assembly, labor and mounting parts are required. For example, it would take about four 5-by-5-inch flappers to fill a 1-square-foot area, assuming a 1-inch space between flappers, while it would take nine 3-by-3-inch flappers to fill the same area. This increased number of flappers translates to more than double the amount of assembly time, labor, mounting hardware, etc.
Flapper finishing
Flapper elements produced from pre-finished sheet material, such as anodized or painted aluminum, typically are more cost-effective than post-finished flappers. The type of finish influences the overall cost of the kinetic façade. For example, standard anodize and painted colors will be more economical than exotic colors and multi-step coatings.
Finish on back of flappers
Finishing the back-side of flappers can incur additional costs because it requires the use of extra material and resources. Anodized flappers will have both front and back faces coated with the same process. Painted flappers, on the other hand, can accommodate different coatings on the front and back face. To reduce overall cost, a wash coating on the back side of the flapper may be acceptable when the rear face is barely visible.
Supporting structure finish
In addition to the finish on flapper elements, the finish applied to the supporting structure, (i.e., the horizontal and vertical mounting rails), influences the cost of the total façade system. A darker, low-sheen finish typically is applied to the supporting elements to accentuate the aesthetic quality of the flapper elements. These framing members usually are painted.
Building spans and loads
The required span and environmental loads can affect the weight and size of the kinetic façade’s structural elements. This can, in turn, impact the cost of the system.
Mounting hardware
The mounting hardware and anchoring systems of the flapper elements depend on the required span, deflections and building substrate materials. This hardware can consist of embeds integrated into the building structure or post-applied anchors supplied by the façade system manufacturer.
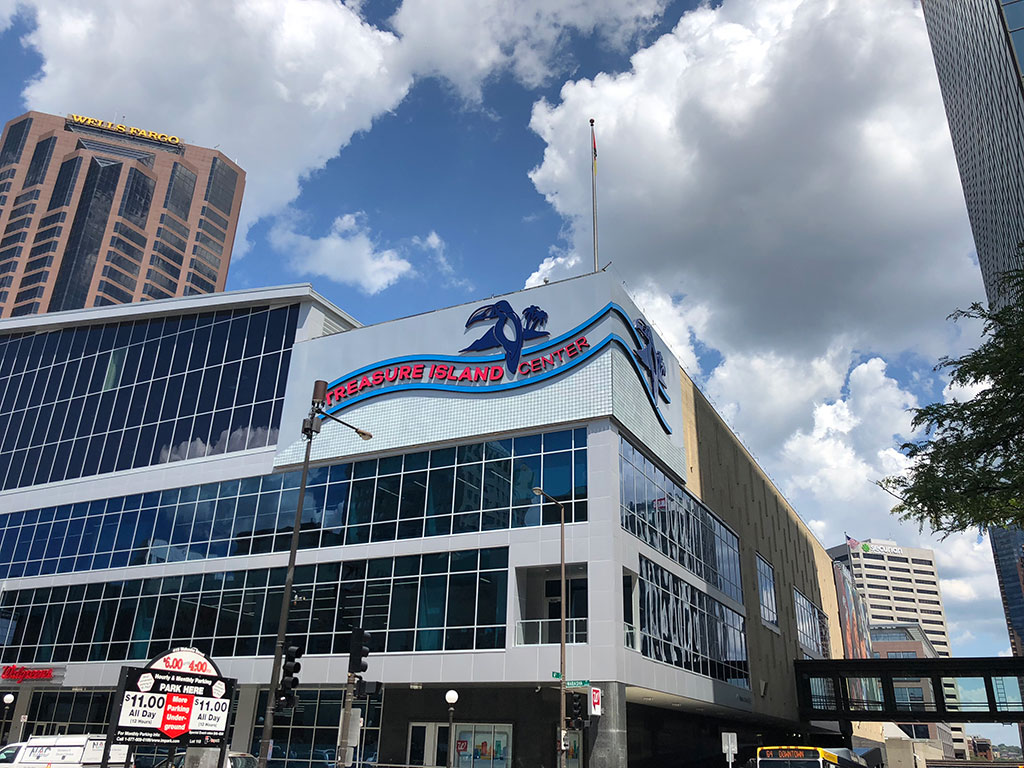
Treasure Island Center
Client: St. Paul Port Authority
Architect: Collaborative Design Group, Inc.
Installer: Albrecht Sign
Façade manufacturer: EXTECH
Manufacturer and installer considerations
Given the complexity of kinetic façade systems, seek an experienced designer and manufacturer to participate early in the project’s design. Look for one offering preliminary cost estimating, mockups and a variety of fabrication and installation options to meet each project’s functional and aesthetic requirements. Some manufacturers will manage all aspects of the installation process, providing a single-source price directly to the building owner or general contractor.
For maximum cost efficiency, a kinetic façade manufacturer may be willing to deliver its services solely as a material supplier. With this solution, materials are provided directly to a local installation contractor already involved with the project, such as a glazier, curtainwall installer, roofer or general contractor. Startup supervision and initial training for installation crews may be included as part of these services.
In this role as material supplier, the façade system manufacturer may offer pre-bid support. Generally, this involves presenting the system, its installation processes and other relevant documentation to prospective contractors.
Once the bid is approved and the contract awarded, a successful installation of a kinetic façade is measured in terms of time, cost and quality. It requires the synergistic coordination of various activities including design, engineering, testing, fabrication, delivery and installation. This begins during the conceptual design phase, with the development of the project schedule.
Typical project durations range from 12 to 20 weeks from the time of award. The type of overall design, the complexity of the kinetic elements, and the scope of the installation are some of the factors that can affect this timeframe. For large-scale kinetic façade systems, delivery schedules often are phased at various construction stages to allow a continuous stream of material through the duration of the installation. This phased method of delivery avoids potential damage to components stored on site and helps conserve space by limiting site laydown and storage areas.
The kinetic façade installation typically is arranged as one of the final undertakings during building construction; thus limiting the exposure of the façade elements to potentially damaging activities from adjacent trades.
With the installation complete, minimal manual cleaning is required. For most kinetic façade systems, periodic inspections for issues, such as storm damage or vandalism, as well as mounting connection checks are recommended.
With early involvement and ongoing collaboration between the designer, specifier, installer and manufacturer, wind-driven kinetic façade systems add a dynamic and distinctive element to parking garages, retail centers, museums, sports arenas, theaters and other building structures.
About the authors
Jim Leslie is the general manager of EXTECH/Exterior Technologies, Inc., in Pittsburgh, leading the company’s mission to improve lives through innovation in daylighting systems, natural ventilation and other building envelope systems. Working closely with architects and specifiers, Leslie and his team redefine the intersection between the natural and built environments with wall, window, skylight, canopy and custom systems, such as dynamic façade designs. Leslie has a bachelor of science in mathematics from Penn State University and is a member of the American Production and Inventory Control Society (APICS). He can be reached at jleslie@extechinc.com.
Kevin Smith is a Registered Architect, and leads EXTECH’s team of architects and engineers as director of product application and development. He brings more than three decades of experience in designing commercial, civil, industrial and transportation projects, as well as daylighting, static and kinetic façades. He earned a bachelor of architecture from Carnegie Mellon University. He can be reached at ksmith@extechinc.com.