As you look up to see a tiny figure leaving a smoke trail among the clouds, rarely does one consider how much time and work is required to manufacture a plane. Boeing has been a long-time pioneer in the aircraft manufacturing industry, founded more than a century ago. Today, the company has manufacturing facilities in more than nine states, and 10,000 Boeing jetliners are currently in service worldwide.
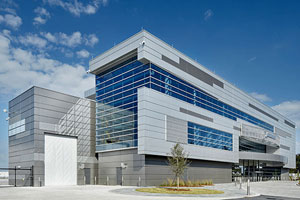
Photo credit: CENTRIA
In 2011, Boeing opened its second assembly and delivery facility, spanning 58,000 square-feet across three floors in South Carolina. In an effort to streamline the production process and increase delivery time, plans were made to renovate the Charleston Boeing Delivery Center into a state-of-the-art aircraft paint facility in 2014. Prior to the development, Boeing was forced to send their aircrafts out of state to be painted, delaying the production process and final product. The new 256,000 square-foot facility now stands 10 stories high and reaches almost two football fields in length, making it large enough to host two Boeing 787 Dreamliners at the same time.
Calloway Johnson Moore & West of Lexington, PA was hired as the architecture firm for the development. Due to the heavy industrial use of the facility, CENTRIA’s Formawall® Dimension Series® insulated metal panels were chosen to provide thermal efficiency as well as wind and flame resistance. The panels offer superior weather protection, and deliver a sleek façade. The CENTRIA metal wall panels were coated in Sherwin-Williams Coil Coating’s Fluropon® Classic metallic coating in the colors Pewter and Silversmith – providing an air-like aesthetic to the facility’s exterior with the main overcast gray tone perfectly accented by the dark gray.
CENTRIA’s EcoScreen® Perforated Screenwall product was also selected to provide a 10 – 40 percent open area for an airy aesthetic that controls light and air movement, while covering unsightly HVAC equipment.
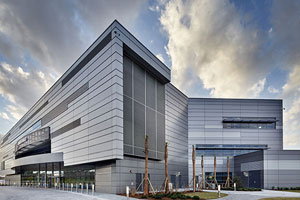
Photo credit: CENTRIA
Sherwin-Williams Coil Coating’s Fluropon coatings are a staple in the industry, formulated to stand up to harsh weather conditions and protect against chalking, fading and ultraviolet rays. Fluropon Classic is a high performance 70% PVDF coating that consists of a pearlescent color coat and a protective clear topcoat. The special metallic-effect color coat combined with a clear coat accomplishes an added shine and shield, providing the Boeing Delivery Center with a vibrant three-coat finish.
The Boeing assembly building in Charleston was the company’s first 100 percent renewable energy site, with up to 20 percent of the energy supplied by more than 18,000 thin-film solar panels on the roof. The energy efficiency benefits of CENTRIA’s metal wall panels and the Fluropon Classic coating will help continue the standard for the new Charleston Boeing Delivery Center, while maintaining an aesthetic that reflects the nature of its work.
Project Overview
Project: Boeing Delivery Center; Charleston, SC http://www.boeing.com/
Year: 2016
Coatings provider: Sherwin-Williams Coil Coatings; Minneapolis, MN http://www.valsparcoilextrusion.com/
Metal panel manufacturer: CENTRIA; Moon Township, PA http://www.centriaperformance.com/
General Contractors: Turner Construction Companies, Charlotte, NC
http://www.turnerconstruction.com/office-network/charlotte; and BE&KGreenville, SC http://www.bekbg.com/
Architect: Calloway Johnson Moore & West; Lexington, PA http://www.cjmw.com/
Metal panel installer: SPS Corporation; Raleigh, NC http://www.spscorporation.com/