First, a definition
Put simply, concrete is a mixture of cement, water, fine aggregates (like sand) and coarse aggregates (like gravel). Cement and water make up a paste that helps fresh concrete flow. A chemical reaction between the water and cement causes the paste to harden, binding the aggregates into a solid, stone-like mass.
So how do you transform this mixture of ingredients into a thing of beauty? By choosing the right coloring and finishing techniques to suit your vision and need.
Finishing methods
The way concrete is finished – what happens to it after it is poured or formed – can make the same mix of cement, water and aggregates look incredibly different. Here are some descriptions of different finishing techniques.
Trowel or broom The most basic concrete finishes are trowel or broom finishes. Both are executed when the concrete is placed, before it cures. Hand troweling gives a hard, burnished, smooth surface; a simple and familiar look for interior concrete. Brooming creates a bit of texture (more or less, depending on the tool used) and imparts some slip resistance for outdoor installations. A subtle pattern can be achieved by brooming different sections of the slab in different directions.
Texturing Imprinting or “stamping” fresh (uncured) concrete gives the surface more texture and pattern. Imprinting is popular for creating the look of bricks, tiles or stones, but it also can be used to create more whimsical designs – dinosaur footprints or a sandy beach, for example. Natural elements like saw grass or leaves can be used to imprint concrete, but most often an imprinting tool is used. One popular tool is an embossing skin, a flexible mat placed randomly over surface to give the appearance of a stone slab. Pattern tools mimic repeatable designs like bricks, cobblestones or tiles. Imprinting tools can also be supplied or custom designed to stamp animal tracks, leaves or any other random design element or accent.
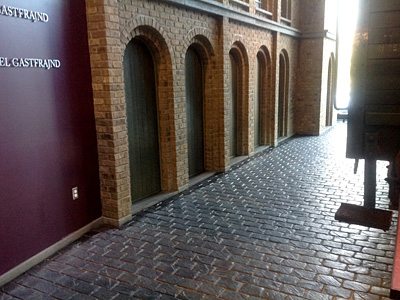
Holocaust Memorial Center with LITHOTEX® Pavecrafters® – Cobblestone Running Bond. Courtesy of L. M. Scofield
Imprinted concrete is significantly enhanced by the artful use of color. Coloring specifics will be covered in the next section, but basically the techniques and materials especially well-suited to imprinted concrete include integral color, dyes, dry shake color hardeners and antiquing release materials that add an accent or shadow at the same time they facilitate release of the imprinting tool from the concrete surface.
Imprinting enhances the beauty of pool decks, patios and parks. This use of pattern and color helps designers harmonize these areas with surrounding structures and forms.
Another dramatic way to give concrete texture is sandblasting. Typically used outside, different looks can be achieved by varying the grit of the sand and the pressure and duration of the application. Sandblasting not only alters the texture of the concrete surface, but it can make a surprising difference in the appearance of the color as it changes the way light bounces off the surface as well as exposing some of the light aggregates in the concrete mix. The most common coloring method used with sandblasting is integral color, an admixture added to the concrete mix to impart color through the entire slab.
Impactful, one-of-a-kind spaces can be created by juxtaposing sandblasted with smooth concrete, or integrating other pattern elements such as sawcuts or stencils.
Exposing aggregate using a chemical surface retarder is another way to impart texture. In contrast to sandblasting, this process leaves the aggregate intact, so colors are more distinct and less muted. Retarder is spread over the surface of fresh concrete and the level of exposure is controlled by the length of time the retarder is left before rinsing. Carefully selecting aggregates gives designers the opportunity to create special effects. For example, options include integral color admixtures, gravel in a color that complements the concrete, mica, marble chips or even glass. Aggregates can even be hand-seeded to create special color patterns.
Grinding and polishing This technique gives interior floors a hard surface polished to the desired level of sheen. Because it is executed after the concrete is cured, it can be used on new or existing concrete. Simply put, the concrete is treated with a chemical densifier and then mechanically ground with tools using progressively finer grits. Ground and polished concrete, whether new or old, can be colored with reactive or water-based stains or dyes. Other coloring systems can be used under certain circumstances, described below.
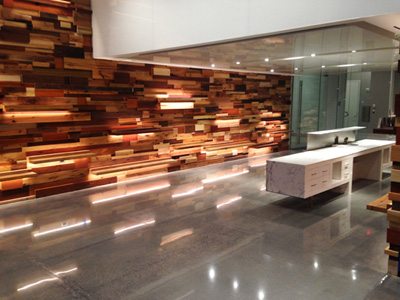
Alexandria Restaurant/Philadelphia Polished Concrete with SCOFIELD® Formula One™ Liquid Dye Concentrate. Courtesy of L. M. Scofield.
Designers should think of polished concrete in three grades. Grade one is the lightest cut, just polishing the top surface and leaving a light sand finish. This gives the most uniform appearance. New concrete that is to be polished to this grade can be colored with a dry shake color hardener or integral color admixture.
Grade two is a medium cut that delivers what is called a salt-and-pepper finish due to the exposure of fine aggregate. In new concrete the desired color can be achieved by selecting an integral color and complementary or contrasting aggregate. Thinking beyond gravel, designers have used elements that uniquely represent their clients – things like gears, marbles, small toys, pottery shards and colored glass.
Grade three exposes large aggregates. This can invoke the look of natural stone or terrazzo. Again, new concrete can be designed with integral color and selected aggregates. Polishing old concrete to this degree can reveal dramatically beautiful natural stone aggregates, often from local, long-gone quarries.
Why should architects, designers or specifiers choose ground and polished concrete? Besides being beautiful, polished concrete has distinct advantages over other flooring materials. Because it is so dense and hard, it delivers a durable, slip-resistant finish. It is simple to maintain and avoids the potential for VOCs, mold and allergens associated with carpet. And high-gloss, lightly colored polished concrete has the potential to reflect light, reducing lighting requirements for greater LEED compliance.
Another benefit of grinding and polishing existing concrete: in the mantra of “reduce, reuse, recycle,” this does all three. Reusing an existing floor eliminates the need to produce, transport and install new flooring materials, reducing the environmental impact. It also eliminates demolishing and disposing of useful materials. From updating a retail or manufacturing space to renovating or restoring a historic building, choosing to grind and polish an existing concrete floor is both artistic and environmentally sound.
Overlays
The last technique to be discussed here is not as much a finish as it is a fresh start. Cementitious toppings or overlays cover an existing surface with a fresh layer of material. Toppings are applied in two layers – a base coast and a finish coat – over existing concrete. With the right underlayment and surface preparation toppings can also be applied over other surfaces including wood and tile. The finished overlay is generally only 1/8 to 3/16 inch thick, making this system a good option for renovation. It also allows designers to get the look of concrete in new construction weight would preclude the use of a traditional concrete slab.
Cementitious toppings can be finished like any other new concrete surface – troweled, broomed, textured, sawcut or polished. And they can be colored with any technique used for traditional concrete – integral admixtures, color hardeners and liquid releases, stains and dyes.
Coloring techniques
Coloring is where the design versatility of concrete is most evident. And both ultimately depend on the designers’ vision and the customer’s end-use requirements.
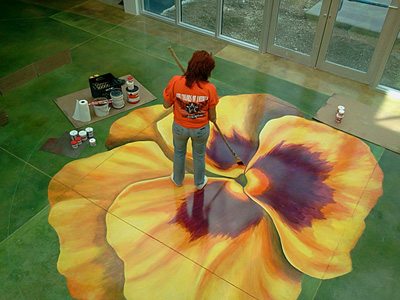
Costa Farms/Alternative Floors with LITHOCHROME® Tintura™ and SCOFIELD® Formula One™ Liquid Dye Concentrate. Courtesy of L. M. Scofield.
The methods that will be described below include
- integral color – an admixture integrated into the concrete mix or cementitious topping for consistent color throughout the whole pour;
- dry shake color hardener – a powder broadcast over the surface of fresh concrete;
- antiquing release – a powder or liquid used with imprinting tools on fresh concrete to prevent tools from sticking and add accent colors to an imprinted pattern;
- reactive stain – a liquid that penetrates the surface and reacts with chemicals in cured concrete to create variegated, mottled color;
- water-based stain – similar to reactive stains but more opaque, with the potential for brighter colors;
- concrete dyes – applied during polishing, dyes are used for bright colors;
- and colored restoration products – a penetrating water repellent that restores faded colors in concrete slabs and pavers.
Not every coloring method can be used on every kind of concrete application. Figure 1 is a quick reference for understanding where they can be used.
More detailed descriptions of each coloring method follow.
Integral color Powder or liquid admixtures added to a concrete mix before pouring result in consistent color all the way through the slab. Integral coloring admixtures also increase the strength and durability of concrete over its life.
Integral color imparts a single color to the whole mix, but using multiple mixes gives designers a whole palette to create a pattern defined by sawcuts and joints.
Using different finishing techniques can vary the appearance of integral colors. For example, exposing aggregate or sandblasting to different depths changes the saturation of the color. Adding a second color by using an imprinting tool with an antiquing release adds accents and dimension to an integrally colored pour.
Admixtures tend to give concrete muted colors that are similar to natural stone, so integrally colored concrete is a good choice for artistic effects intended to mimic nature, such as stone paths or walls.
Because integral color is less labor intensive, and so more cost-effective, than some other coloring methods, it is particularly attractive for adding color to large installations. Lighter colors also have high SRI values and diffuse reflectivity, potentially earning LEED points for reducing heat island effects and lighting requirements.
Dry shake color hardener This powder is broadcast over the surface of fresh concrete to deliver permanent, uniform, consistent coloring and an abrasion-resistant surface. Highly opaque, color hardeners offer a broad color range, including custom colors, from subtle to vibrant, making them a good choice for harmonizing with colors in structures and other design elements. Multiple colors can be layered to create variations. They resist fading and UV damage for stable coloring that conforms to ASTM C-979 and lighter colors can reduce lighting requirements.
Color hardeners can help keep concrete cooler to the touch. They are also impermeable, making them desirable for water features.
Dry shake color hardeners are often used for imprinted concrete, in concert with antiquing release agents.
Antiquing release Release agents are bond breakers that prevent imprinting tools and embossing skins from sticking to fresh concrete. They can be clear, but using colored antiquing release powders add subtle, realistic color effects to the textured concrete. Because it settles in the grooves and valleys of the imprint, it adds the impression of depth and dimension.
Usually applied in a darker color than the underlying material, they add depth and variation to concrete colored with integral color or dry shake color hardeners, making imprinted textures look more natural. Standard and custom colors are available and their stability conforms to ASTM C-979.
Dry shake color hardeners and antiquing release agents can be used for cementitious toppings as well.
Reactive stain Sometimes called acid stain, this penetrating liquid is applied to a cured concrete surface or cementitious topping colors. The color is created by a chemical reaction between the stain and the calcium hydroxide in the concrete. Because they are more or less transparent, reactive stains let the beauty of the underlying concrete and aggregates show through. By the same token, they let blemishes and faults show through as well, and may even exaggerate them.
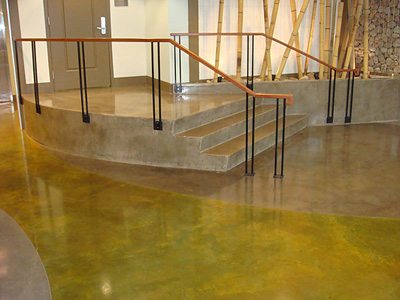
Indigo Hotel/Triad Construction Services with LITHOCHROME® Chemstain® and LITHOCHROME® Tintura™ Stain. Courtesy of L. M. Scofield
Reactive stains deliver mottled or variegated color, unique to each slab. The palette runs to classic browns, greens and blacks. Stains can create distinctive marbleized, faux or distressed finishes. Multiple colors of stains can be applied adjacent to or overlapping with each other for more variation. Stains can also be diluted for less intense color.
Reactive stains are long-lasting, but they barely penetrate the surface, so sawcutting, grinding and polishing should be done before applying the stain. Also, they should be sealed to keep them looking new.
This coloring method is popular for renovating old spaces, elevating the concrete to a colorful design element. Because it is very durable as well as beautiful, it is often used in commercial and even manufacturing spaces as well.
Reactive stains are most often used in ground and polished floors, but can be added to horizontal interior trowel and broom finished floors and cementitious toppings too.
Water-based stain For a more opaque appearance and for brighter brights and darker darks, designers should consider water-based stains. A light application tones and unifies the surface. More opaque color is achieved with higher coverage rates. The product’s opacity makes it useful for blending patches into older colored floors. The wide range of color choices includes reds, greens, blues, pinks and yellows.
With these colors, water-based stains are especially prized for creating works of art – representational pictures like florals or sharply delineated geometric patterns. They’re also useful for beautifying infrastructure like highway walls or water tanks. Artistic effects can be created by spraying, layering, spattering or sponging multiple colors on top of each other.
Concrete dye Liquid dyes are applied to concrete during the grinding and polishing process to color the surface of interior installations. They do not react with components in the concrete, but color the surface in bright, very opaque colors. Dyes range from vivid colors – reds, yellows, blues and greens – to earth tones. The color is highly controllable, so dyes are a good choice for matching corporate designs like logos. Dyes can cover flaws and give new life to old concrete.
Colored concrete restoration A penetrating water repellant designed to restore colored concrete, this product can be used on pavers as well as concrete slabs. It evens out the color so the surface looks refreshed and uniform. It also improves the color intensity of exterior concrete that has faded. It can bridge the inconsistencies between mismatched pours or between high traffic areas and less worn places. They also add a measure of color to uncolored concrete.
You have probably deduced by now that not all coloring methods can be used with all finishing techniques. Figure 2 is a quick guide to which techniques work together.
Bottom line – why design with concrete?
Concrete is beautiful, versatile, durable, affordable, environmentally friendly and easy to maintain. And Scofield, the most experienced manufacturer of architectural concrete systems, can help you realize your artistic vision with results you can trust.
About L. M. Scofield Company
Scofield is the oldest and most trusted name in architectural concrete coloring, texturing and performance. For 100 years we’ve set the standard for the industry by pioneering and developing engineered systems that allow repeatability and consistency, batch-to-batch and project-to-project. Working with and educating architects, interior designers and landscape architects, we’re the most specified manufacturer in the industry.