Whether you are designing to meet the latest energy code for extreme weather conditions or for LEED certification, the goal is likely the same – to get the highest possible thermal performance out of your building. This benefits the building owner and occupants alike, reducing the energy bill and providing a more comfortable place in which to work and live.
There are multiple avenues an architect can take to achieve a high level of energy efficiency. Architects have come to know advanced glazing as their go-to resource for thermal performance improvement. However, in recent years advancements in fenestration have given framing a new place in a building’s energy efficient design.
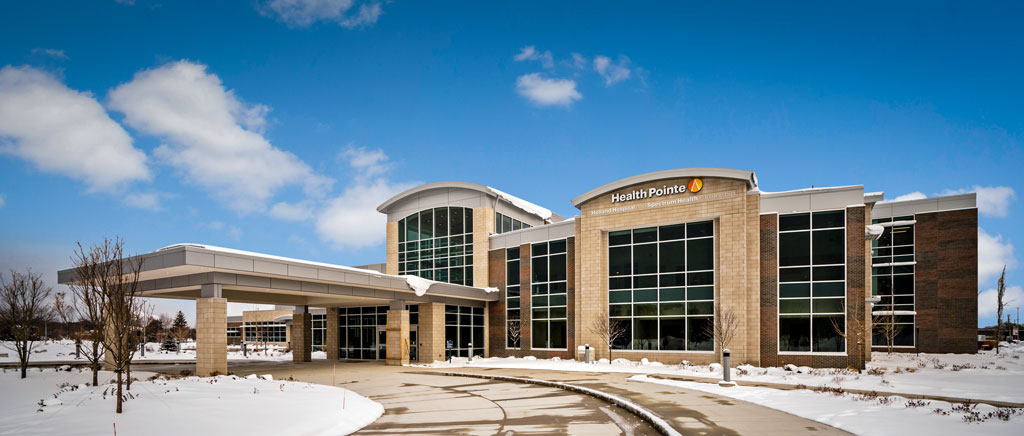
Photo: Joseph Stanford Photography
A Simplified History: Framing Systems, Glazing + Energy Codes
Advanced glazing solutions, such as low-e glass or argon-filled glass, work to improve the center-of-glass (COG) thermal performance value. However, the system’s thermal performance is less effective where the captured glass edge meets the supporting frame. This makes the type of framing system and the performance of that system critical when considering the energy performance of a building.
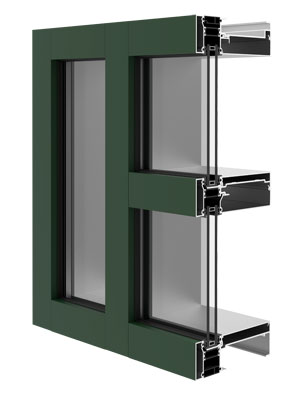
YCW 750 XT IG – Inside Glazed Curtain Wall System
Framing systems have traditionally been known for having high thermal conductivity, making them more vulnerable to heat gain and loss, as compared to other elements of the building envelope. Thermal breaks were first introduced to help solve this issue nearly thirty-five years ago, as part of the response to the energy crisis in the 1970’s. Over time framing manufacturers continued to advance the technology and systems to meet evolving energy codes; however, if an architect sought to exceed code, it primarily looked to the glass industry to make the difference. Advancements in glass were extensive — air fills including argon, krypton and xenon, as well as soft coat low-emissive (LowE) glass were introduced, and gained significant traction as architects looked to improve the energy performance of buildings. However, over the past ten years the fenestration industry has taken particular note as energy codes have become more stringent.
Energy codes in the U.S., even state-written codes, typically follow the International Energy Conservation Code (IECC) or ASHRAE 90.1. These codes continue to be revised every three years to keep up with building technologies, and to inspire new ones. Both organizations have also written sustainable building codes that states can adopt, for example the International green Construction Code (IgCC) and ASHRAE 189.1. Each state has the authority to adopt any energy code or develop its own based on its specific climate. For example, Florida Building Code continues to be tailored specifically to meet impact requirements given its coastal climate and vulnerability to natural disasters like tropical storms and hurricanes. The continuous evolution of these energy codes has spurred new technologies for commercial framing systems.
Advancements in Commercial Framing Systems
Thermal breaks and condensation resistance are two of the main factors that have since seen significant advancements in commercial framing systems.
Thermal Breaks
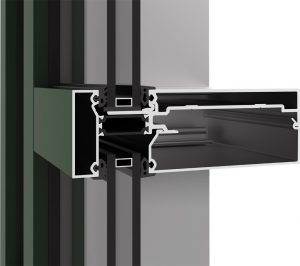
YCW 750 XT IG – Inside Glazed Curtain Wall System
Thermally-broken framing systems have become more advanced within the industry. For years aluminum framing manufacturers have used Polyamide 6.6 with 25 percent glass fiber structural struts or a pour and debridge process to create these thermal breaks and improve energy performance. By crimping the struts between to separate extrusion or filling a channel in the aluminum extrusion with a polyurethane material and then removing (debridging) the bottom of the channel, the outer aluminum is isolated from the inner aluminum within the glazing system. The latter process economically delivers strong energy savings but has been met with some controversy with lack of adhesion and “dry shrinkage” issues in the past. This has prompted some manufacturers to incorporate technologies such as ThermaBond PlusⓇ, used to improve the adhesion of the polyurethane material to the aluminum extrusion; and the use of Mechanical Lock ProfileTM which adds slightly more urethane poured over the lanced extrusion to form a stronger structural bond. These added technologies resolve adhesion and dry shrinkage and deliver proven performance over the life of the building.
Additionally, new uses of material have been discovered, particularly in curtain walls, by using polyamide to replace the traditional aluminum pressure plate. Fiberglass has also been more commonly used in thermal breaks over the last ten years, to amplify energy savings. A polyamide composition, for example, helps insulate 500 times better than aluminum, providing structural and thermal performance that yields performance increases of up to 20 percent reduction in U-factor using the same LowE glazing materials.
Condensation Resistance (a bonus feature)
Condensation resistance is also critical to the thermal performance of a building. The American Architectural Manufacturers Association (AAMA) developed the condensation resistance factor (CRF) as a method of rating the ratio of the surface to ambient temperature difference. The addition of thermal breaks in metal and non-metal material provides a small pathway for heat transfer, which has helped to mitigate condensation and thereby increasing a building’s performance.
Currently the AAMA is in the process of writing two additional standards to look at framing, simulate framing in surrounding construction and to build a full mock-up wall to test the condensation resistance and thermal performance, so that architects can understand how the framing will perform on a representative scale before selection or implementation. Additionally, thermal modeling technologies can assist in identifying specific framing attributes to take into account where condensation is a concern.
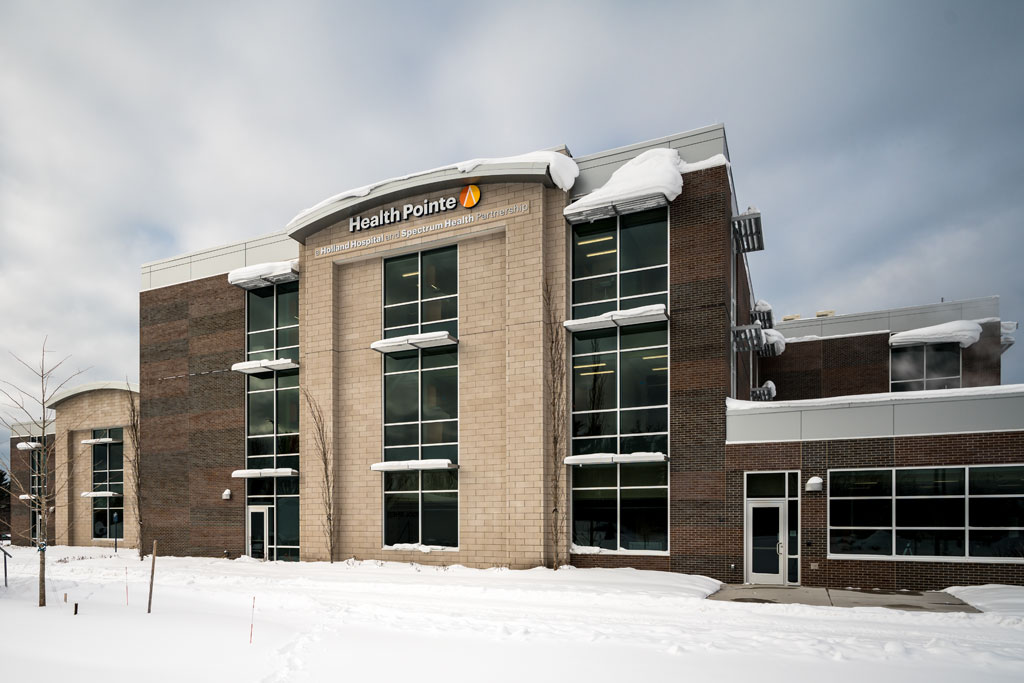
Photo: Joseph Stanford Photography
Sunshades
The use of sunshades in and of itself is not necessarily a modern advancement. Our ancestors used leaves and thatched roofs to protect their homes and maximize energy efficiency. Today’s material-of-choice is aluminum. Sunshades can now more effectively improve occupant comfort and improve a building’s energy efficiency by reducing the solar heat gain coefficient (SHGC).
When coupling sunshades to a curtain wall system it is critical to ensure the anchoring system is thermally broken. By doing so SHGC is reduced and the curtain wall’s U-factor remains intact, rather than taking a five percent thermal performance reduction when using a traditional non-thermal anchoring system. For example, a typical curtain wall system coupled with a sunshade’s non-thermal anchoring system might have a U-factor of 0.47 Btu/hr·ft2·°F. By simply changing out the sunshade’s anchoring system to include a thermal break, the curtain wall system’s U-factor is now 0.45 Btu/hr·ft2·°F.
Sunshades offer design versatility and can often be customized depending on which way a building faces to reduce harmful light, while bringing visible light in to achieve optimal daylighting.
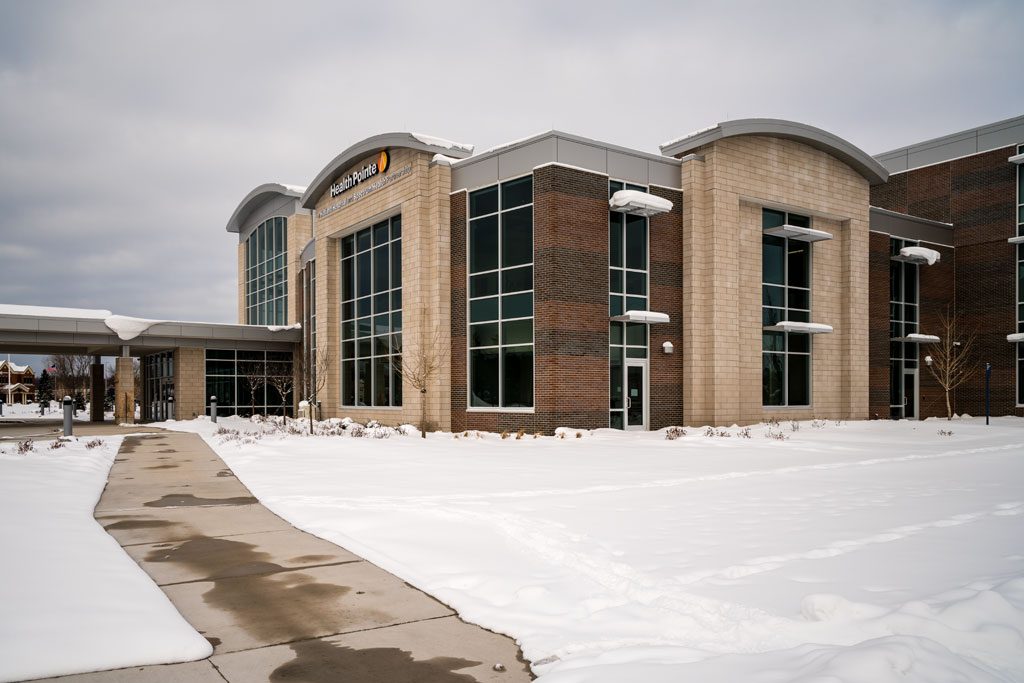
Photo: Joseph Stanford Photography
An Often Overlooked Benefit to Advanced Framing Systems
When using advanced framing systems, it is important to understand an often overlooked, yet key benefit to architects, building owners and occupants alike. Because advanced framing systems work to improve the thermal performance and energy efficiency of the building, the initial tonnage of the HVAC can also be reduced, maximizing upfront cost-savings. Additionally, the cycling time of the HVAC is reduced considerably. This translates to less use of the HVAC and ultimately, longer longevity and considerable energy savings. It is a win-win for all involved and should be investigated when designing buildings with high performance framing systems.
Acoustics Matter (An additional Bonus)
Acoustics are an integral part of sustainable design and LEED certification as they relate directly to occupant comfort. While environmental considerations like energy and environment are often considered, it is also critical to consider the noise pollutants of a building. Strong acoustics, particularly in healthcare and education, can go a long way in enhancing the patient’s recovery and classroom learning environment in a building. For example, in a healthcare setting a quiet environment allows the patient to recover with little traffic noise common outside of hospitals. In an education environment, reducing outside noises is critical to a healthy and productive learning environment.
Acoustics can lead to longer longevity and sustainability of a building by creating a comfortable quiet environment over the long-term. Advanced framing can make a strong impact on the acoustic performance of a building. When considering sustainability, be sure to evaluate a framing system’s acoustical performance to ensure the most comfortable environment for occupants and building owners alike.
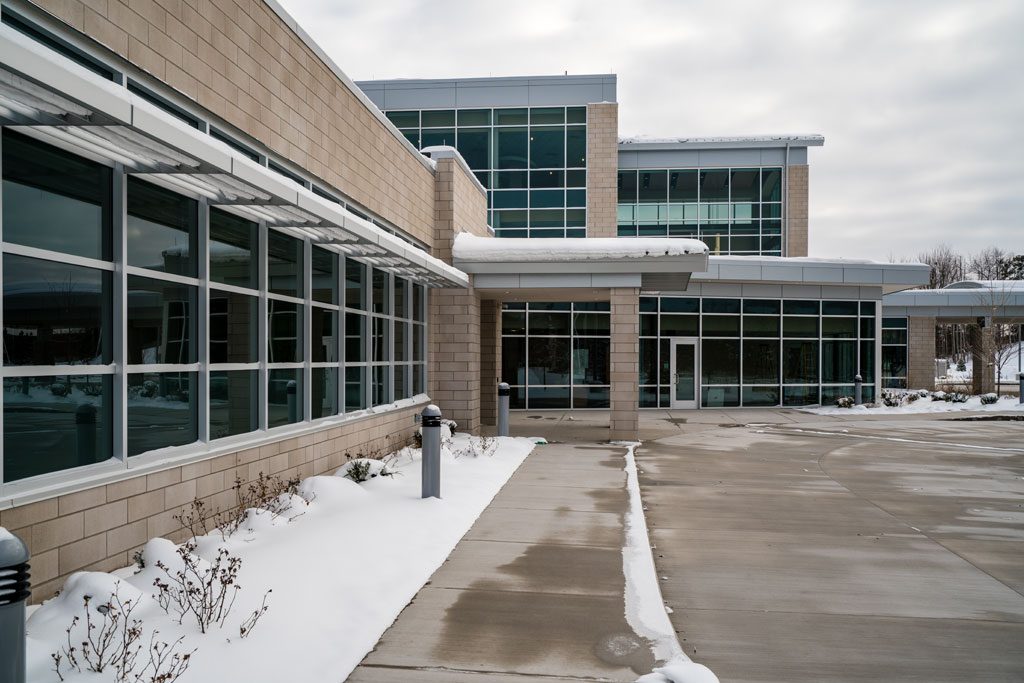
Photo: Joseph Stanford Photography
Framing a Building’s Energy Performance – Now and in the Future
Due to these developments, many framing manufacturers now offer advanced framing with extra thermal performance in storefront and curtain wall applications that achieve U-factors under 0.39 Btu/hr.ft2.oF (W/m2.oC) to meet and exceed codes and to save energy, without the need for advanced glazing. Upgrading the framing system of a building in most cases results in double the thermal performance, as compared to just adding argon-filled glass to a standard system. While the upfront costs may be slightly more than an argon-filled glass, the framing system is designed with the entire building in mind, rather than the individual component, so as to ensure lasting performance for the life of the building.
About the author
David Warden is the enerGfacade® brand manager for YKK AP America’s family of energy efficient fenestration products, and is responsible for spearheading marketing efforts both externally and internally for the product line. He has been with the company for more than 17 years, and is beginning his eighth year as the enerGfacade brand manager. David has also served as a Product Marketing Engineer, where he provided technical research and reviewed outside engineering and testing as it related to product initiatives and energy modeling. Before that he worked for three years as an Applications Engineer in YKK AP’s DirectTech and the five years prior to that he worked as a Special Projects Engineer in the company’s Technical Administration department. He is a LEED ® GREEN ASSOCIATE and an NFRC Approved Calculation Entity (ACE).
About YKK AP
YKK AP America Inc. is a technology-oriented manufacturer of commercial façade systems and residential doors and windows. With every finished good, we push the boundaries in next generation manufacturing and create value for architectural applications. Driven by a desire to provide exceptional service in our markets, YKK AP America builds upon our foundation of advanced engineering, vertically integrated manufacturing, and customer focus to deliver the highest level of quality at a competitive price. Headquartered in Austell, Ga., all building products are manufactured in our world-class production facilities located in Dublin, GA. and Macon, GA. YKK AP America Inc. is a subsidiary of YKK Corporation of America, whose parent company is global manufacturer YKK Corporation of Japan. For more information, visit ykkap.com and follow us on Linkedin.com.