Pursuing the cutting edge in research and education has always been a focus at the University of Arizona—located in Tucson. And this intent was evident when the University first set out to build a new hub, on campus, to house bioscience research themes that included work on biosensors, bioimaging, bioinformatics, healthy aging, genomics technology, and precision medicine. The building itself is a joint collaboration between the University of Arizona Office for Research, Discovery, and Innovation and the University’s Department of Health Sciences. It was designed by ZGF Architects and BWS Architects, and the general contractor was DPR Construction.
The goal of the building was to house 50 faculty members and over 300 graduate students, post-docs, and technical support staff. Some of these individuals would be moving from other places on campus to pursue interdisciplinary research, and many would be new to the University—especially recruited because of the promise associated with this new space. The building was also set to be home to a clinical-certified genetics facility focused on testing tumor biopsies in order to set the best course of treatment for individual patients.
Ultimately, the demand for innovation was primary in this construction project. And the teams associated with the groundbreaking and realization of this building had to be able to rise to the challenge.
A Trifecta of Beauty, Functionality, and Sustainability
With a price tag of $107M and comprised of square footage equaling just over 140K, the new construction of this state-of-the-art facility began in 2015. It was significant in nature and involved many moving parts— and project teams. There was a need for collaboration, communication, and synergy alongside the requirement of hitting quality assurance targets. W. R. MEADOWS was listed in the construction specifications as a potential manufacturer who could get the job done.
“An air barrier and numerous waterproofing products were needed for this project,“ stated Greg Neundorfer, the W. R. MEADOWS salesperson in charge of this project. “There were also multiple transitions between these products that needed to be addressed.” Products used in this project had a tall order to meet; they had to work well with a variety of substrates.
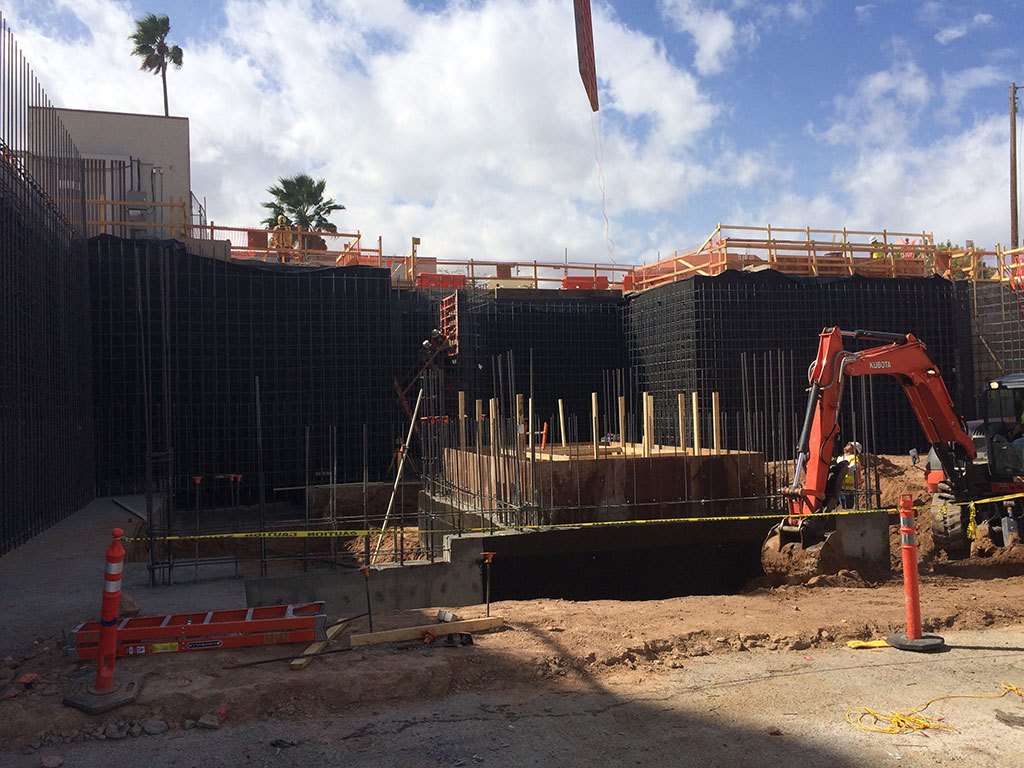
Courtesy of W. R. MEADOWS
Creating the Foundation
Starting from the ground up, the first part of the project was centered on the foundation of the building. “We were confronted with needing multiple forms of waterproofing,” explained Neundorfer. “The first was called blindside waterproofing, also known as preplaced waterproofing. This is present when you are faced with having a hole in the ground that is the size of the building as opposed to being over-excavated. You are building the structure within the exact size of the building itself. So, you have to install a shoring system in order to keep the soil stable. Then, the water-proofing is placed and the concrete is cast against the waterproofing.”
It was Firestop Southwest, the waterproofing installer on this project, who ultimately brought W. R. MEADOWS to the table with the University of Arizona.
Ryan Olsen, started on the project as estimator and project manager for Firestop Southwest. However, after three months he transitioned into a role with Field Verified—a third-party testing agency. “We proposed using W. R. MEADOWS for the waterproofing membrane on both the below-grade and podium decks in lieu of what was specified. The specs, ultimately, had multiple products from varied manufacturers, but we thought it would be better to recommend all W. R. MEADOWS products. I went to U of A and presented to them, explaining what W. R. MEADOWS could do and why we should use them on this project. I told them all the benefits,” Olsen explained.
The University of Arizona ended up agreeing with Olsen’s recommendation and awarded the bid. “I think that using all of the products together is a great benefit to the owner,” said Olsen. “If they ever have an issue, they only have one manufacturer to turn to for maintenance or warranties.”
Another waterproofing product was needed, and had to address positive-side below-grade waterproofing. This is when there is an over-excavated hole and the concrete is cast. The waterproofing is then applied from the backfill side of the hole.
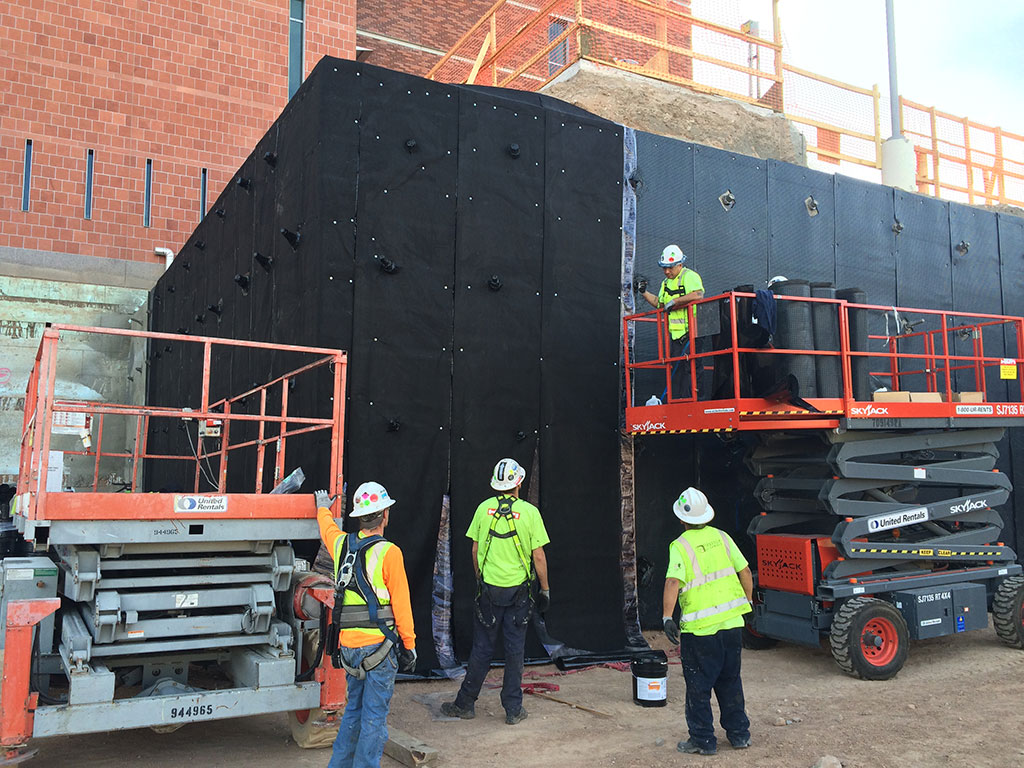
Courtesy of W. R. MEADOWS
Finally, there was also a large breezeway/walkway area that was positioned over the top of the basement. This received two different types of products including a hot-applied material and a cold-applied material.
The blindside product chosen was PRECON®, the positive-side below-grade was MEL-ROL™, the hot-applied material was HRM 714, and the cold-applied material was HYDRALASTIC™ 836. It was noted that the products bond well and work nicely in the Arizona heat.
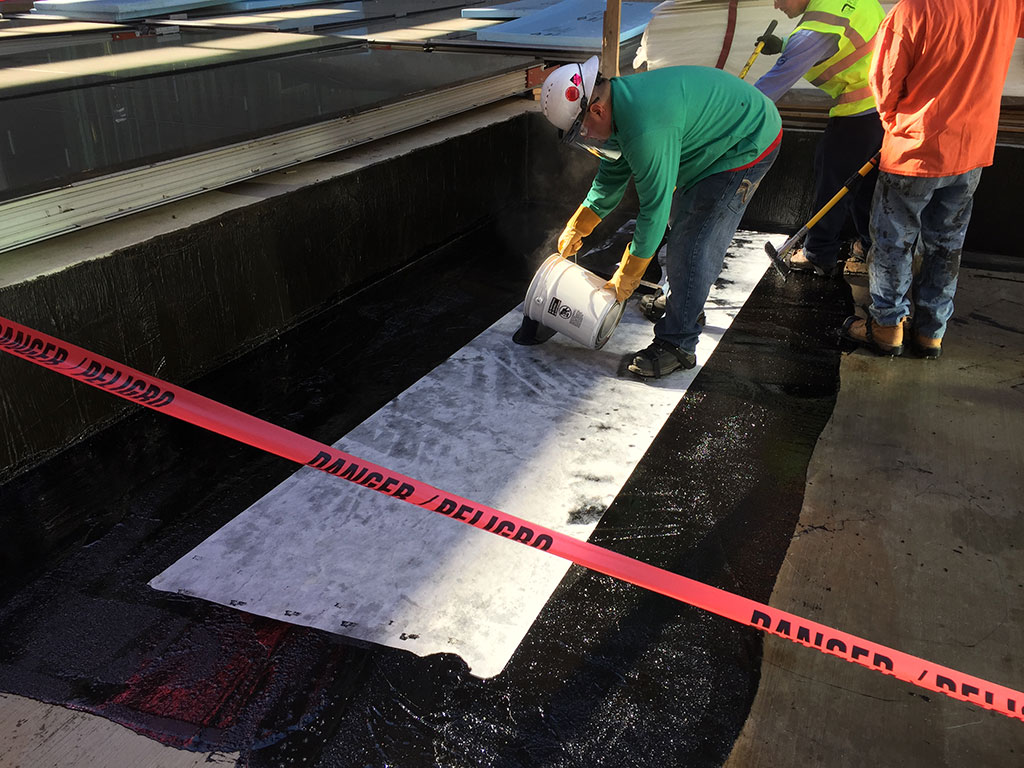
Courtesy of W. R. MEADOWS
A Challenge Arises
The below-grade vertical walls presented the first issue. “The substrates were a little tough,” stated Henry Rocha, the lead installer at Firestop Southwest, “The concrete wasn’t done correctly so it had to be repaired and replaced before we could put the waterproofing down. But Greg was on site the entire time and helped tremendously.”
“It was the manufacturer’s approval process for warranties that was utilized here,” said Tracy Smith, vice president at Firestop Southwest. “Greg assessed the substrate for warranty, and everything was remedied.”
Brian Elliot, a superintendent for DPR Construction, was responsible for handling the foundation structure, air barrier, waterproofing, and anything that had to do with the exterior envelope of the building. Elliot stated, “It was a big job.” He continued, “We had to pour the foundation walls and then had to cast in place elevated slabs that also needed to be poured. So, we had to run the waterproofing up the walls, which then had to tie back into the frame walls. We also had to tie in an existing basement. We had Greg come out and work with us on the strategy here. There was so much going on. From the waterproofing standpoint, it was probably the most technical project I have ever been involved with.”
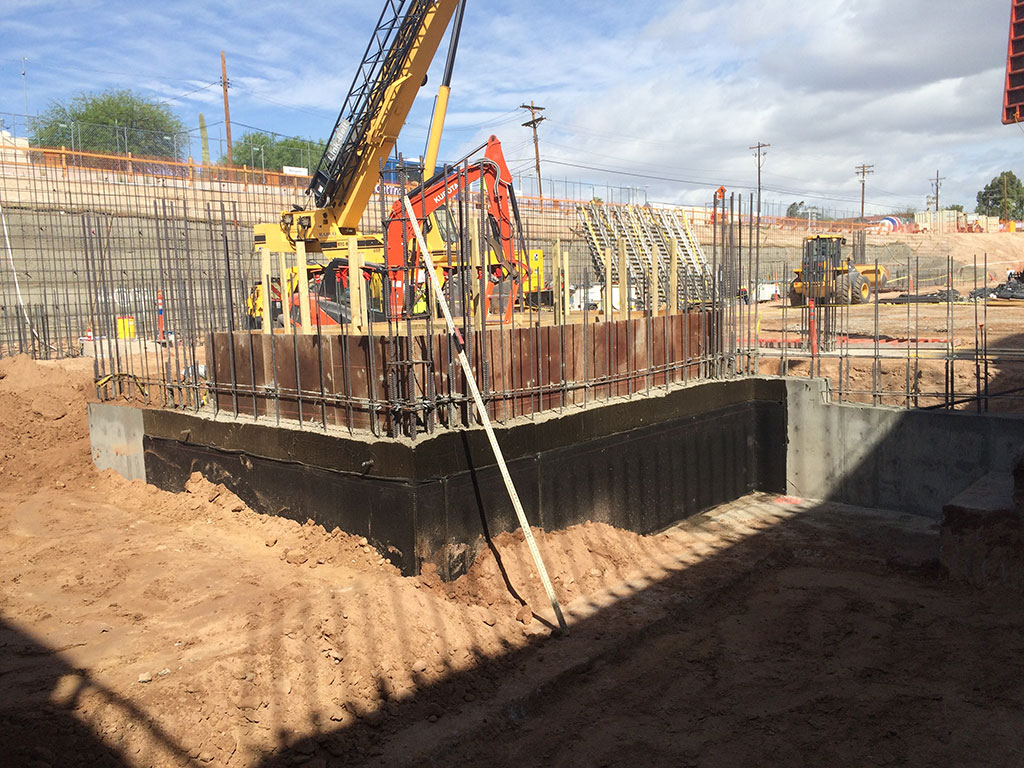
Courtesy of W. R. MEADOWS
Firestop Southwest had a crew of six on site over the course of about a year. There were multiple stages and the company noted that Neundorfer’s experience definitely assisted in the process. “We have a long history with [Greg]. He has been our local rep for a very long time. We love to work with him and have an excellent partnership with him,” said Rocha.
Firestop Southwest also said that there was a considerable time savings experienced by their team, which led to an overhead and cost reduction. “Workers understand how to use the [products] and can handle them well. PRECON is especially easy to use and install. And for an installer, time savings is a huge benefit in this regard—it goes beyond material cost alone. If we can do single source and not have to have multiple manufacturers involved, that is a great perk, too,” said Rocha.
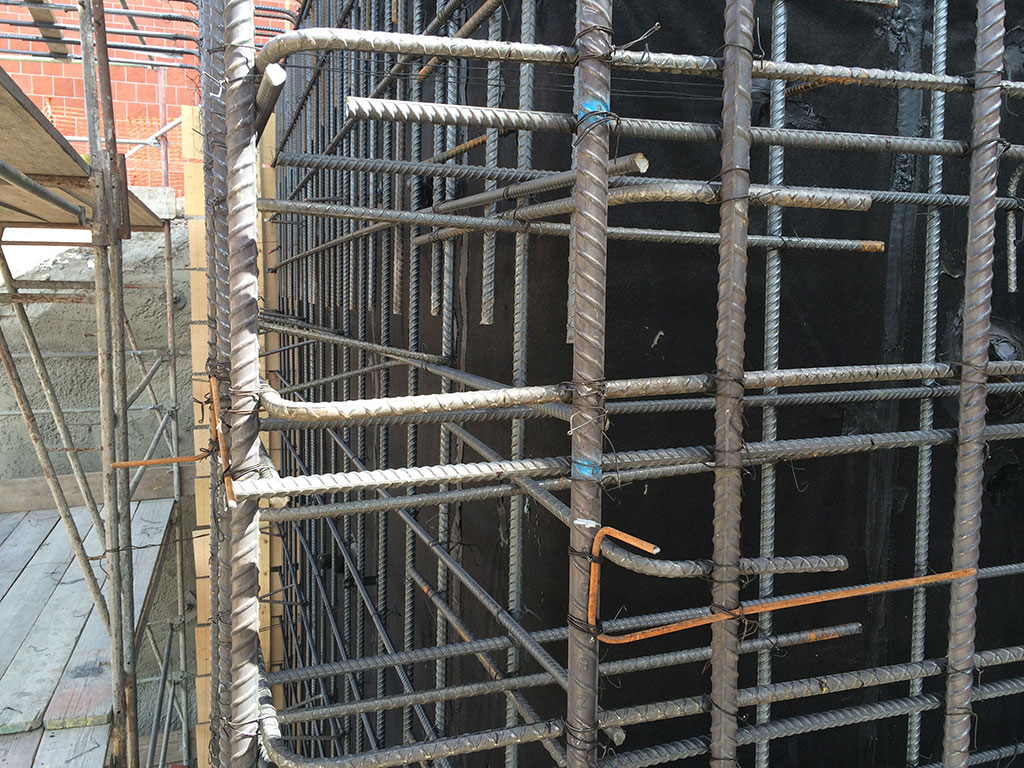
Courtesy of W. R. MEADOWS
The Exterior Façade
AK&J Sealants was the air barrier installer on site. Brian Whited is a partner in the company and was the project manager for the University of Arizona’s Bioscience Research Laboratory. “We have used W. R. MEADOWS air and vapor products—as well as their waterproofing products—on and off for several years now. The Air-Shield LMP is one of our go-to air and vapor products. So, when we were looking at the [U of A] project, that was the product that we referenced in order to price it,” explained Whited. “I believe [W. R.] MEADOWS was actually our approved manufacturer in the spec when we put the pricing together.”
AK& J Sealants was responsible for installing the air barrier on the entire exterior façade of the building and had a crew of five workers at the site on average. The bulk of the façade was metal panel, but there was also some masonry and glass. The air barrier was set to be placed behind these exterior finishes.
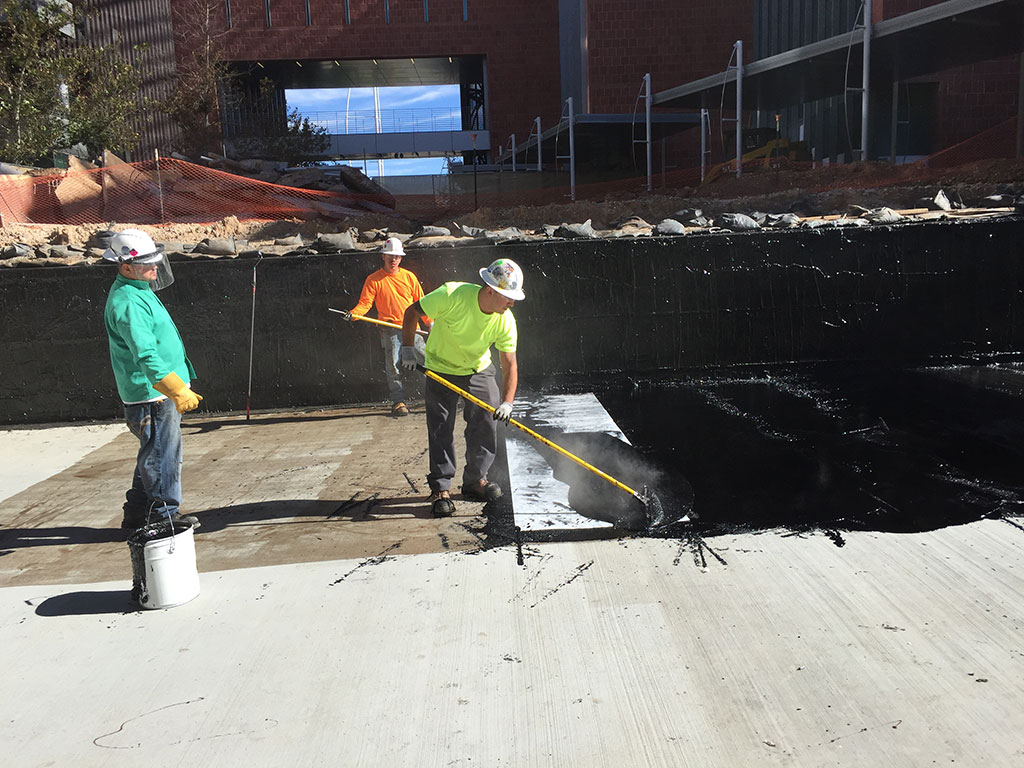
Courtesy of W. R. MEADOWS
“The normal LMP system is a 60-mils system,” said Whited. “However, the specs for this project called for a 90-mils system. It was a bit ‘beefier’ than what AK&J usually handles. However, very few challenges were experienced, and frankly, the majority of issues that did occur were related to scheduling, the fast pace of the project, and the sheer number of people who were present at the site. [AK&J] had to be precise in our installation. There were masons and metalsmiths there who were also obviously wanting to keep to their own schedules and do their work.”
The Man on Both Sides of the Job
If there is one person on this project who had one of the most comprehensive views while on site, it was Ryan Olsen. As stated, he had transitioned to observing and ensuring that the products were installed correctly and properly.
“I was on both sides of the fence here,” said Olsen. “After I left Firestop and started with Field Verified, I ended up having to go over my recommendations and submittal of the W. R. MEADOWS products with my leadership. I discussed all of the reasons why these products were used. What’s more is that instead of only overseeing the below-grade waterproofing, I was actually looking at the entire envelope, including the air and vapor barrier. At the end of the day, everything except the roof was sealed with W. R. MEADOWS products.”
Further to consider Olsen said, was the way all of the products tied together, “It was nice to see how the W. R. MEADOWS waterproofing products would tie in with the air barrier on the exterior walls—and many times in places that would normally prove difficult. The products were able to transition from one substrate to the next. We didn’t have to worry about compatibility because W. R. MEADOWS had that covered.”
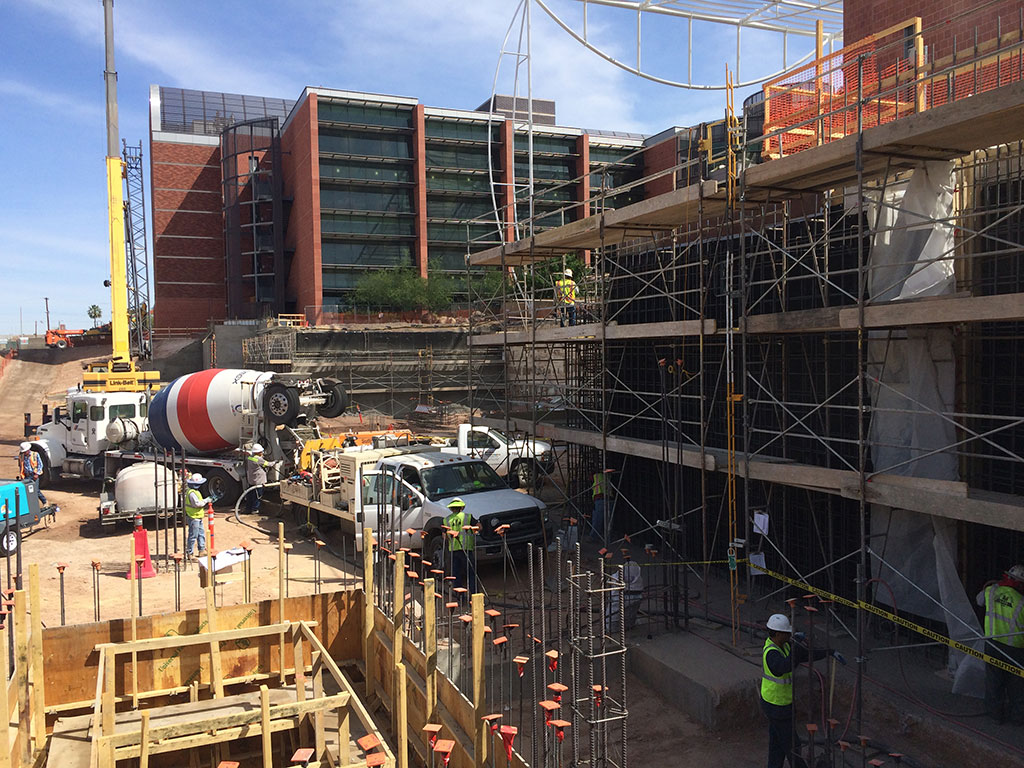
Courtesy of W. R. MEADOWS
Inspecting the Work
Finally, Mike Seal, of the University of Arizona, was the Senior Building Inspector assigned to the Bioresearch Laboratory. He oversaw all of the inspection related to structural, architectural, waterproofing, interior, exterior, and roofing. “Once we got over the first couple of hurdles related to logistics, it was smooth sailing,” Seal said. “We had good installers and a lot of access to product information.”
Seal regularly interacted with Neundorfer as well as Olsen and performed varied forms of testing on both the waterproofing and air barriers. During all phases of the inspections that were conducted, Seal never ran into a situation where W. R. MEADOWS had to fix something. While there were times that the installer had to go back and apply more sealant because of transitions—it was never a state that could be attributed to a product defect.
The Bioscience Research Laboratory project was completed in late 2017. And indeed, the University of Arizona has been satisfied with the outcome of this building. There have been no issues or reports of water intrusion on site. Brent Elliot, of DPR Construction, confirmed this point. “We are still working on campus—and are in and out of this building occasionally. There have been no issues.”
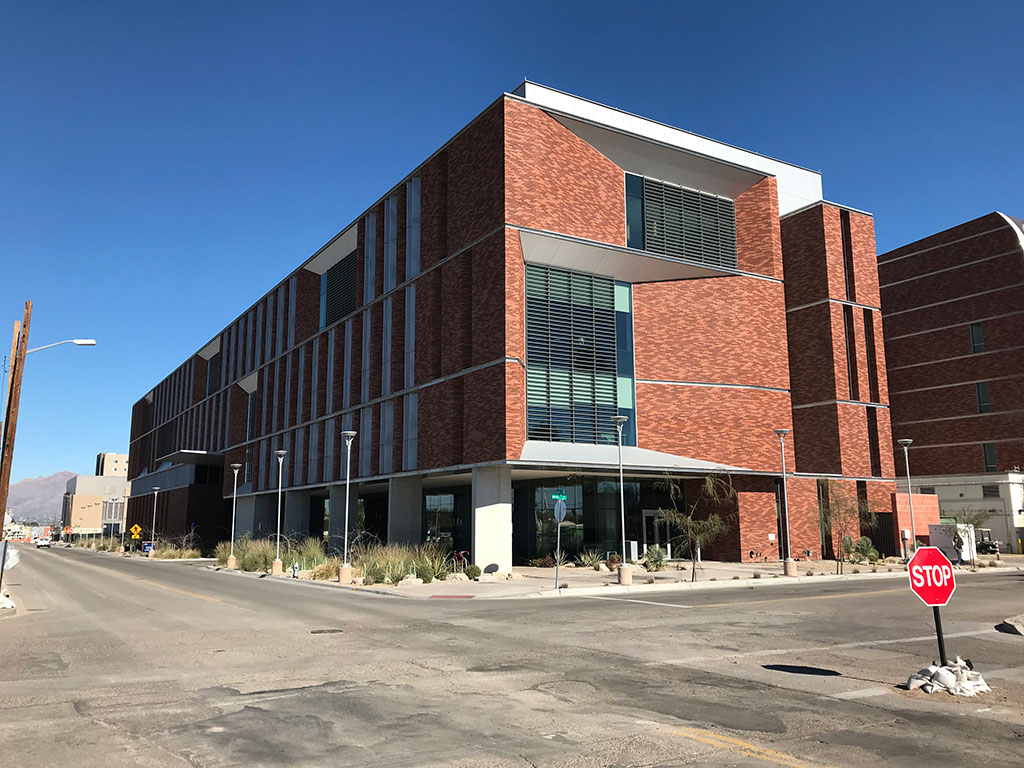
Courtesy of W. R. MEADOWS
A Study on Teamwork
“All around it was a successful project,” said Neundorfer. “Everyone worked well together, from the general contractor on down. I like the whole team effort on this job. I was just so impressed with how we all worked together to get it done.”
And the general contractor confirmed this point. “It was a very good dynamic with W. R. MEADOWS,” said Elliot, “as well as with Field Verified, Firestop Southwest, DPR, AK&J, and the University of Arizona. The entire experience was positive.”
In turn, because of this cooperation, the Bioscience Research Laboratory at the University of Arizona was able to open in March of 2018 and is currently pursuing its mission of bringing creative people together to advance knowledge, find solutions to medical challenges, and improve health outcomes for Arizonans.
About W. R. MEADOWS
Since 1926, W. R. MEADOWS has been a leader in developing products that protect structures from moisture infiltration. From below-grade installations to rooftops and in-between, issue- specific products target and prevent potential, costly problems. Today, patented technologies enable more environmentally effective, efficient designs, and many of our products contribute LEED-certification “green” credits. With nine manufacturing facilities throughout the U.S. and Canada, the materials you need are within easy reach. For additional information, call 800.342.5976 or visit www.wrmeadows.com.