Many product manufacturers rely on factory-applied, durable finishes to maintain the intended look and specified functionality with minimal maintenance. Finishes that offer a unique appearance, texture or weathering performance provide manufacturers with a strategic advantage in appealing to building owners and design professionals who want their buildings to make an enduring, architectural statement.
For high-performance and exterior applications, aluminum product manufacturers choose between polyvinylidene fluoride (PVDF) resin-based architectural painted coatings and anodize finishes. Recent innovations and customizations can expand these finishing options to meet almost any project’s aesthetic, performance and sustainability goals.
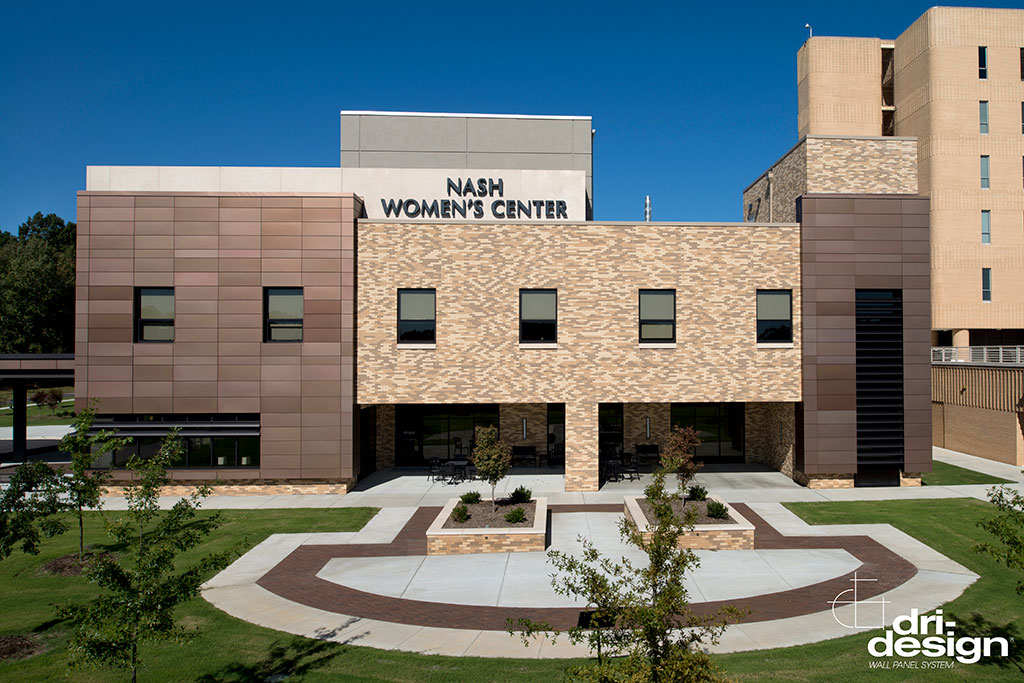
Photo courtesy of Dri-Design and Linetec
Color innovations in anodize
Until recently, the color palette for architectural anodize finishes has been very limited. Anodize finishes emphasize the natural metallic look of aluminum. Exploring beyond clear, bronze and champagne, at least one manufacturer has developed two tawny tones to widen this color range – Copper Anodize and Bordeaux Anodize.
When true copper is impractical, Copper Anodize finish on aluminum can present an economical, close impression. Unlike real copper, the anodize will not patina. It retains its elemental metallic look, exceptional hardness and long-lasting durability.
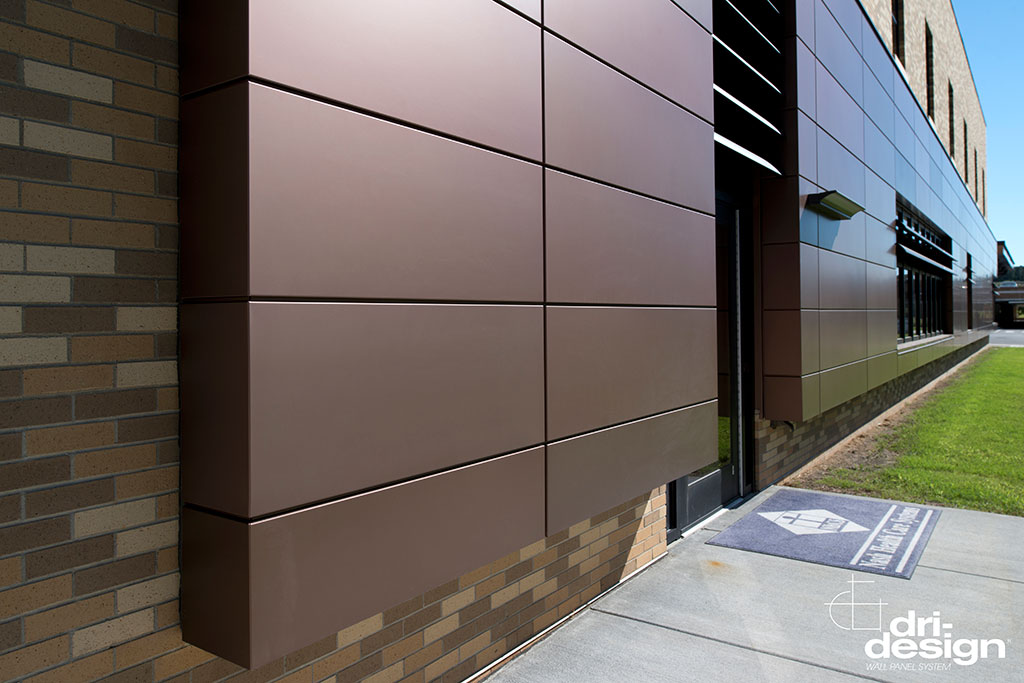
Photo courtesy of Dri-Design and Linetec
Building on the success of Copper Anodize, the newest color innovation is Bordeaux Anodize. This brings a rich, burgundy color to the anodize spectrum. Both Copper Anodize and Bordeaux Anodize provide the versatility to meet either a contemporary or historic aesthetic, while delivering industry-leading performance, without any concern of copper run-off stains on the building’s exterior.
Without diminishing the anodize finish’s performance, a new “brushed” aesthetic option also is gaining interest among architects and manufacturers for aluminum products installed on interiors, storefronts and in highly visible areas. Applied by a finishing provider prior to the anodize process is completed, the brushed anodize appears uniform from a distance. Up close, this brushed technique gives the aluminum a distinctive look. It retains some of its metallic luster, but not all, and offers an approachable and slightly worn-in look.
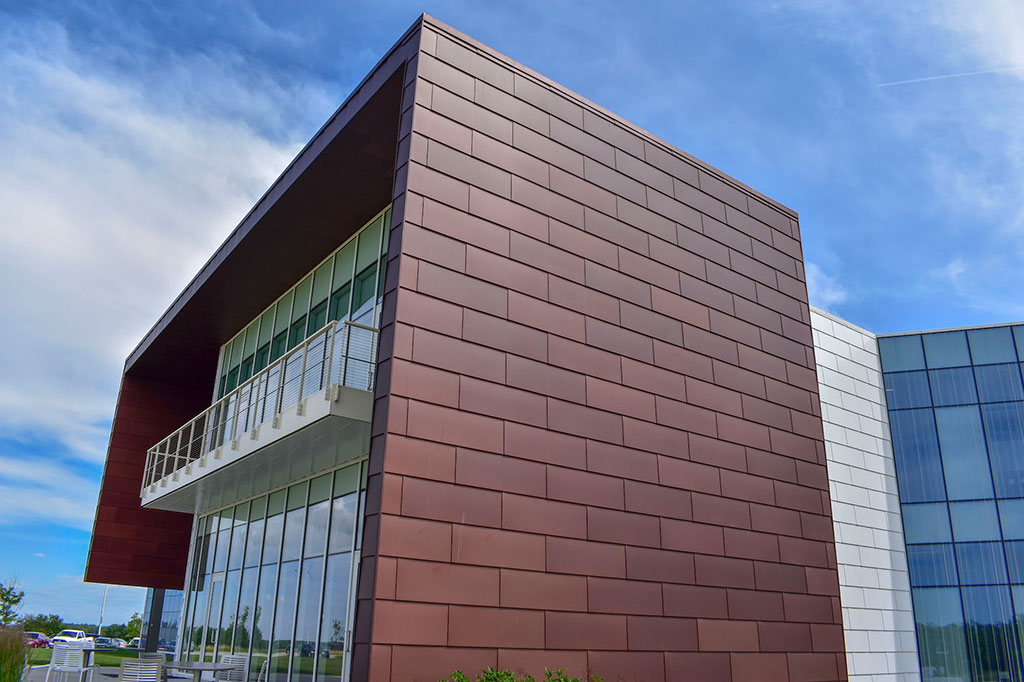
Photo courtesy of Metal Design Systems and Linetec
Sustainability strides in anodize
Anodizing successfully combines science with nature to create one of the world’s best metal finishes by accelerating and enhancing the oxidation of the aluminum substrate. This process produces an oxide film that is uniform, extremely hard and protects the aluminum substrate from deterioration. It provides the highest performance finish for aluminum. Its longevity is its strength. It delivers excellent wear and abrasion resistance.
In the early 2000s, environmentally responsible finishers changed from the traditional caustic etching process to a more eco-friendly etch system. Small surface defects, such as die lines, flow lines or minor imperfections in recycled aluminum billet, are hidden by the improved anodized finish’s “frosty” matte appearance.
Anodized aluminum is an inert, non-combustible material that is 100% recyclable and poses no health risks. There also are no applicable volatile organic compounds (VOCs) associated with this finish type. Recognizing these attributes and anodized aluminum products’ 40-year life expectancy, at least one anodize finishing provider recently earned a Declare Label as Living Building Challenge™ (LBC) Red List Free from the International Living Future Institute.
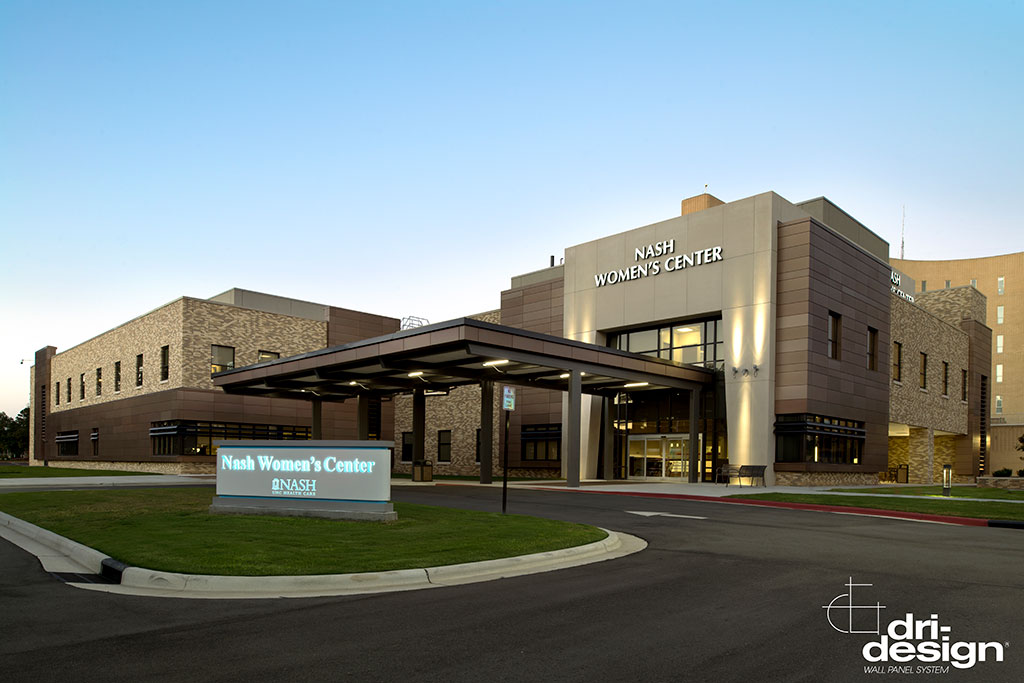
Photo courtesy of Dri-Design and Linetec
Examining building materials’ complex chemical analysis and raw material source location information, the Declare Label provides ingredient transparency in an easy-to-use “nutrition label” format. Declare LBC Red List Free indicates full compliance with the highest level criteria. This means the manufacturer has disclosed 100% of product ingredients plus residuals present at or above 100 ppm in the final product and the product does not contain any Red List chemicals.
Declare LBC Red List Free products are recognized by the U.S. Green Building Council’s LEED Rating System, the International WELL Building Standard, and the U.S. Environmental Protection Agency’s Recommendations of Specifications, Standards and Ecolabels for Federal Purchasers.
Biophilic design in durable architectural coatings
Commercial design trends indicate an intentional shift to incorporate reminders of the natural world within the built environment. Following these biophilic principles, wood, terra cotta and marble patterned finishes can be applied to architectural aluminum products to mimic the beauty and warmth of the genuine material without the actual maintenance.
Today’s finishing providers can replicate a global forest of wood species choices from Knotty Pine to Dark Walnut to Teak. Produced using a powder coat, dye sublimation technique, the newest variations also can make the wood grain finish look aged, reclaimed or distressed. Some finishing providers can even imitate the depth and simulated grain of wood without the splinters. Regardless of the species or its simulated years and texture, these architectural aluminum finishes save the potential headaches of rotting, warping, pests, refinishing, repair and other issues associated with real wood.
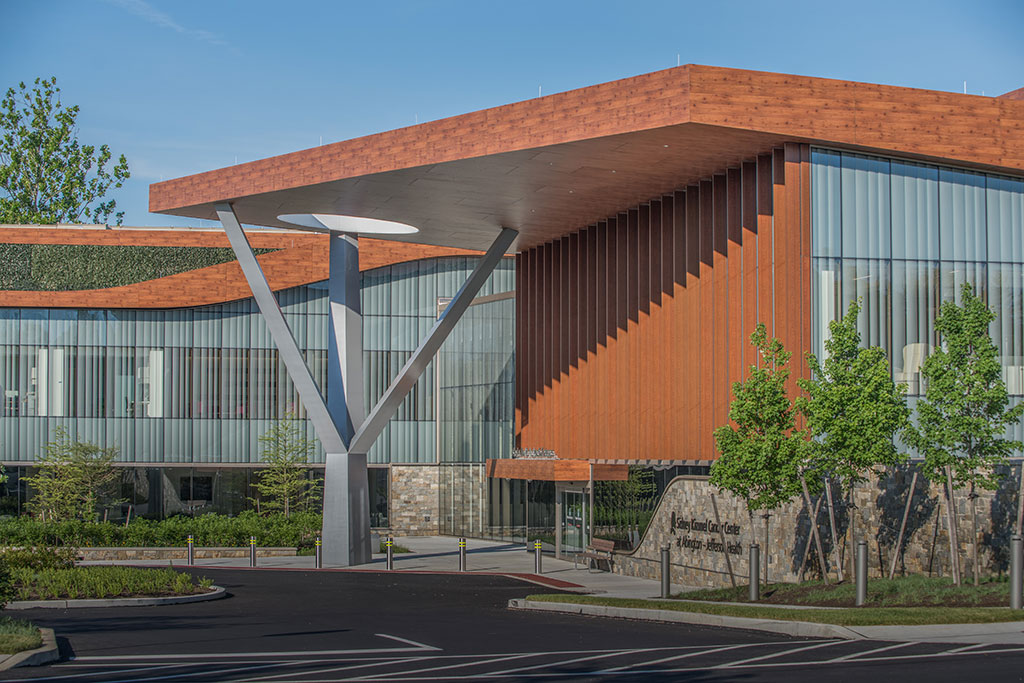
Asplundh Cancer Pavilion’s 86,000-square-foot outpatient center in the suburbs of Philadelphia. Photo by Joe C. Garvin, courtesy of Linetec
While maintenance may not be the key issue, terra cotta, marble and natural stone masonry may be out of reach for many buildings’ budgets. Conveying the elegance of these luxurious materials at an economical price point, some finishing providers are achieving a similar appearance on aluminum wall panels and trim.
Spattercoat finishing can mimic marble, stone, brick and more. Customized to the project’s individual criteria, the specialty finishing process begins by first painting the entire exposed aluminum surface with the specified PVDF resin-based undercoat color. On top of this, additional colors of paint are layered using a spattercoat technique. The paint spatters can be many or few, large or small, thick or thin to produce the desired three-dimensional, textured effect.

Photo courtesy of Linetec
Finishes also can enhance the biophilic and sensory experience with texture. Adding fine aggregate to high-performance PVDF resin-based architectural coatings creates a tactile quality. Terra cotta painted colors gain authenticity with a gritty stone-like feel. Finished aluminum products also are lighter weight than real stone, which also makes them easier to install. These building products can come in a large variety of shapes and sizes, and be delivered in a short lead time.
Stellar attraction with metallic and mica coatings
Whether inspiration comes from a night sky full of stars or a hand-tailored suit of fine silk, mica and metallic coatings now can bring sparkle, shimmer and shine to almost any color. A dynamic finish choice, the reflective quality of these specialty coatings appears to change throughout the day and the seasons.
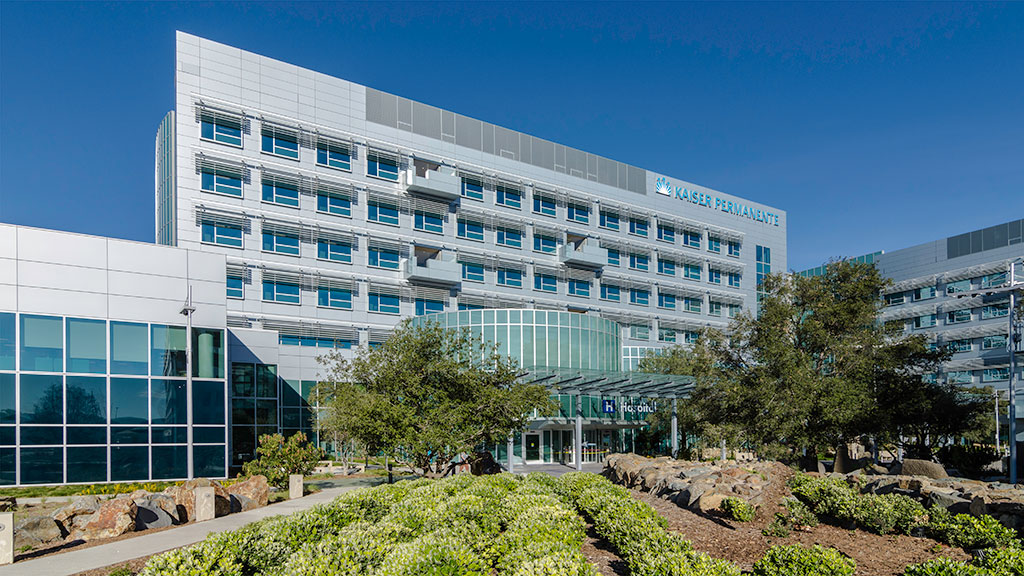
Kaiser Permanente San Diego Medical Center. Photo by Brennan Photo and Video, courtesy of Quality Metalcrafts and Linetec
The light reflectance of the aluminum flakes within the mica and metallic coating gives the finish its lively appearance. The size and reflectivity of the flakes in the coating, their orientation and the degree to which they are all oriented in the paint coating will affect the brightness of the color. Typically, darker colors do not provide as much sparkle and bling as the lighter colors. Be aware that bright, semi-transparent colors, such as silver metallics, also tend to present the greatest potential for variation.
A full-service, single-source finishing provider can provide manufacturers with the most effective options to reduce visible variation, especially when applying these coatings on large surfaces like a metal panel system.
Attractive in Terra Cotta and Regatta
As a world-renowned program, the Iowa Culinary Institute (ICI) at Des Moines Area Community College (DMACC) provides high-end culinary experiences and serves students, staff and visitors. Reflecting ICI’s reputation and revitalizing its facility for future growth and success, Shive Hattery Architecture + Engineering designed a fresh, contemporary look for the existing structure and its two additions.
Today, the updated building encompasses 34,000 square feet and features an attractive, modern façade that resembles terra cotta, but actually is aluminum. The specialty finish applied by Linetec to Dri-Design’s wall panel system mimics both the look and the feel of natural terra cotta.
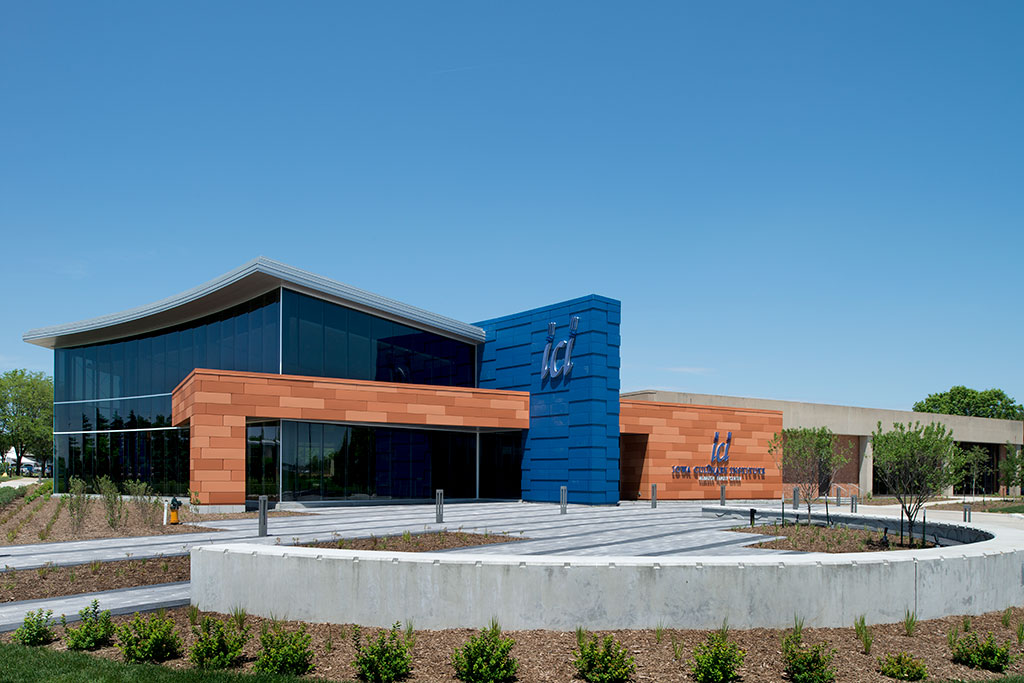
Iowa Culinary Institute (ICI) at Des Moines Area Community College (DMACC). Photo courtesy of Dri-Design and Linetec
Shive Hattery found its inspiration in a building located to ICI’s west that used a true terra cotta tile. To achieve a similar aesthetic, Linetec applied three different colors of terra cotta finishes to Dri-Design’s 0.080-inch aluminum wall panels: Terra Cotta Armagnac, Terra Cotta Mountain and Terra Cotta True Penny. SGH Inc. installed these in a planned “random” pattern to further replicate the desired, natural look of stone.
In addition to the terra cotta textured finishes, Linetec painted 5,038 square feet of Dri-Design’s Shadow Series panels in Pewter and Regatta color mica coatings. The vibrant blue Regatta corresponds with the college’s brand identity.
“The design team wanted to match that look with something that installed easily, was cost effective and has low maintenance,” explained Dri-Design.
Compared with true terra cotta, aluminum wall panels painted with Linetec’s terra cotta textured finish are a more economical option and delivered in a short lead-time. SGH Inc.’s installation team also appreciated the lighter weight of aluminum versus stone.
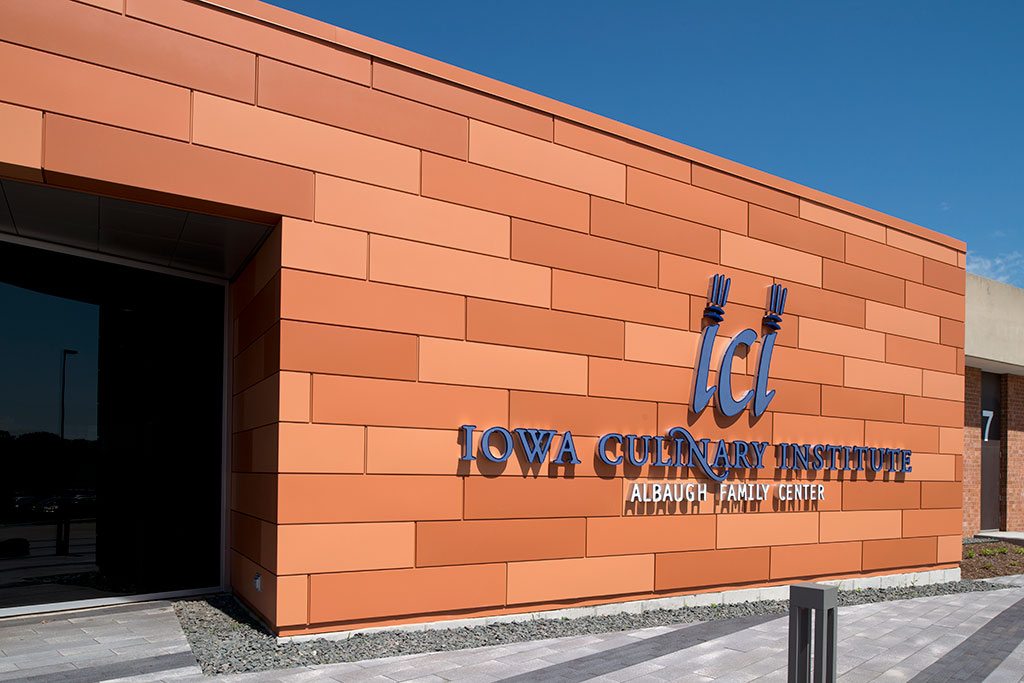
Photo courtesy of Dri-Design and Linetec
Using 70% PVDF resin-based coatings achieves the signature color and the highest levels of performance suitable for exterior architectural aluminum products. Like all 70 percent PVDF coatings applied by Linetec, the terra cotta finishes meet the requirements of the American Architectural Manufacturers Association’s standard AAMA 2605. Tested to exhibit outstanding resistance to humidity, color change, chalk, gloss loss and chemicals, these durable finishes need minimal maintenance to keep their intended appearance.
Completed in the spring of 2016, ICI’s redesigned entryway, lobby and pre-banquet space set a tone complementary to gourmet dining experiences. The north addition houses the new million dollar mechanical equipment systems. The south addition provides additional classroom, office and conference room space, as well as 7,500 square feet for an indoor common space capable of hosting large-scale events.
“The Iowa Culinary Institute (ICI) at DMACC is a visual statement of a building,” said Paul Rathjen, architectural designer at Shive-Hattery. “Both the client and contractors were very satisfied. It’s crazy, but it’s cool. While visually it demonstrates a unique design, it’s really not that complicated. Everyone loves the color, and it pops from the street.”
Rob Denson, DMACC President and CEO called the $5.5 million project “one of the most attractive and functional culinary facilities in the nation and a great place for our many guests to visit.”
Custom colors and finishing applications
When one of the 50,000 colors available still does not quite match, finishers with an in-house blending laboratory can scan samples to color match anything from a piece of metal to a swatch of fabric, and then formulate the recipe of tints and bases to create a match. Paint coatings can align with an organizational logo, school colors, team uniforms or company brand.
Finishing service providers with computer-controlled mix and match color systems and quality assurance processes may be approved partners with high-performance paint manufacturers. These systems, processes and partnerships not only achieve a precisely verified color match, but do so with confidence that the color will be consistent and meet the paint specification for the project’s requirements.
Climate and geography are the most significant factors influencing the exterior performance of an aluminums finish. For interior requirements, one of the top considerations will be the likelihood of contact in high-traffic environments such as retailers, schools and entertainment venues. For curtainwall, storefront, entrance, skylight and window systems, both exterior and interior needs must be reviewed. The exterior surface is almost always the surface with the highest performance requirement, which usually sets the overall finishing specification.
Some finishing providers can accommodate different finishes on each surface of the aluminum framing system when thermal strut is used. Finetuned to meet the functionality and color schemes of each room, these dual-finish applications also can support value-engineered approaches to staying within budget and on schedule.
About the author
Tammy Schroeder, LEED® Green Associate, serves as marketing manager at Linetec, a single source solution and the nation’s largest independent architectural metals finishing company. With 20 years of experience in the finishing industry, she shares her knowledge of liquid paint coatings, powder coat and anodize with architects, specifiers and architectural product manufacturers in commercial and residential markets. She can be reached at tammy.schroeder@linetec.com or by calling 800-236-2589.
Read more articles by Tammy Schroeder:
“High-performance architectural coatings for extruded aluminum”
“Architectural color trends: conceptual inspiration to practical application“