Building Enclosures require proactive actions by each member of the Design and Construction Teams to deliver a building that meets stated performance requirements. Air Barriers are a critical component to meeting those requirements.
This document addresses ten of the most Frequently Asked Questions (FAQs) that Architects, Engineers and Construction Managers/General Contractors ask with respect to air barriers. The answers that follow provide insight for these team players to minimize building enclosure risks and provide assurance that their projects are proactive in meeting the performance requirements.
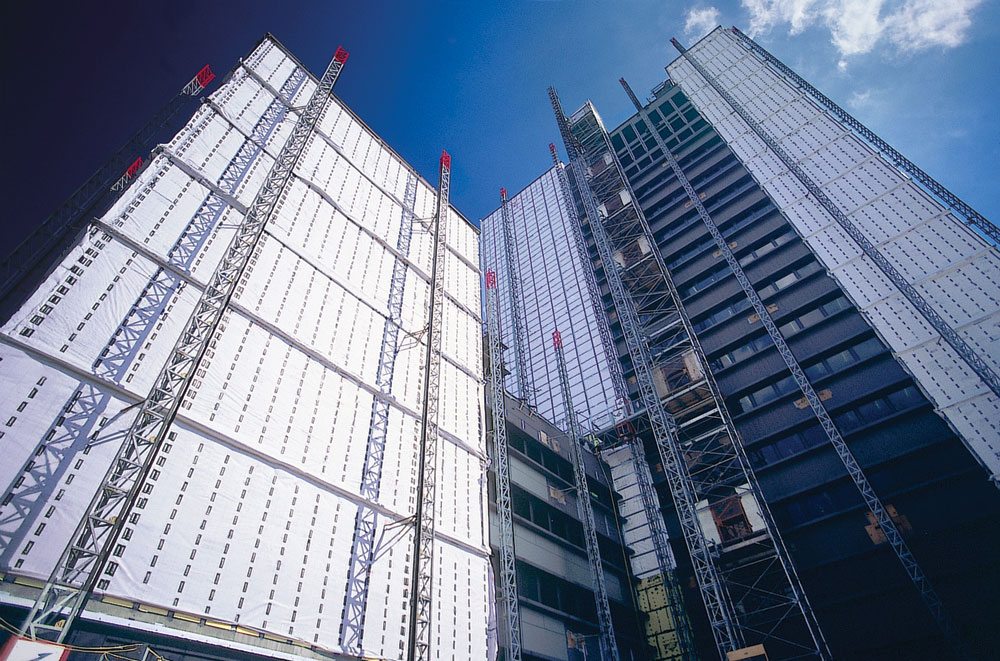
Application of commercial building wrap. Credit: Dupont
1) How do the Design, Bidding, Pre-construction and Construction processes impact air barrier performance?
Design is critical to the specification of the air barrier material to match up with the project location, occupancy, schedule for installation, and integration of the project specifications to assure that the continuity of the air barrier is maintained from design thru construction. The project specification would include the performance field testing requirements per the ABAA Quality Assurance Program (QAP).
Bidding is critical to the selection of a CM, GC and air barrier installer that have the collective experience and knowledge to plan and implement a successful air barrier installation on the specific project pursuant to the specified ABAA QAP.
Preconstruction is critical to the air barrier to provide the submittals, shop drawings, mock up, first work, and coordination scheduling for all trades and the training/demonstration during the mockup performed by the air barrier installation crew to assure proper transitions and terminations.
Construction is critical to the air barrier for scheduling, work sequence, weather protection, protection from other trades, and maintaining continuity of the air barrier including at the interfaces of the waterproofing, fenestration, penetrations, parapets, and roofs.
Each of these processes are equilaterally important to the performance of the air barrier and the attainment of the stated objective for the building. The design should be established, critiqued with input from related trades, and executed with a verification plan to ensure that the end product meets the owner’s performance requirements.
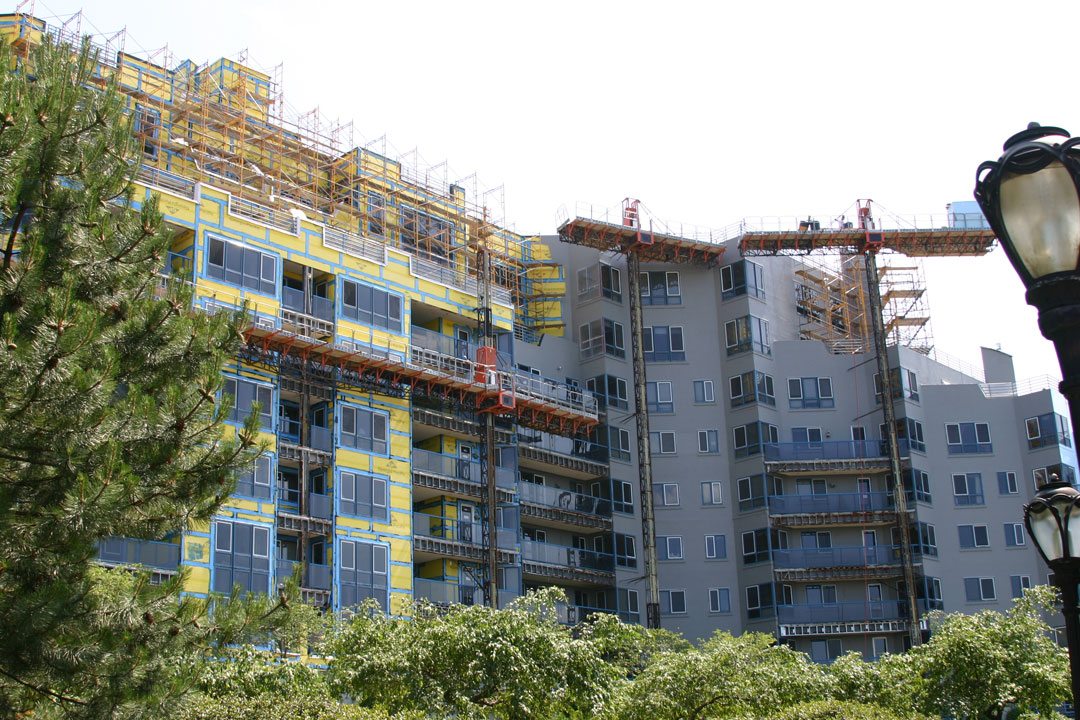
Marina Bay retrofit project, Boston. Credit: Henry Company
2) Do building envelope specifications need to be integrated with the air barrier specification?
Yes, all specification sections for work that interface with the air barrier system must be integrated to establish and maintain the integrity and continuity of the whole building air barrier strategy. For example, cladding and insulation manufacturers/subcontractors need to know about air barrier manufacturer requirements for penetration treatments, adhesive compatibilities, etc. Lack of an integrated specification to assist in contractor coordination may lead to inadequate substrate installation, incompatibilities in product selection, or inadequacies in the installation, all of which affect the final performance of the air barrier.
3) What strategies can be implemented in the project specification to facilitate the CM/GC’s ability to enforce specified installation instructions and to ensure compliance with the specified performance criteria before covering the air barrier with an exterior cladding?
Assurance that the air barrier system will meet the required field performance starts with a quality set of details and coordinated technical specifications, including the ABAA Quality Assurance Program, to help place the general contractor in the best position to provide a successful installation. However, a number of strategies can also be employed in the “Quality Requirements” specification (Section 014000) to ensure coordination and verification of the required field performance of the air barrier. These strategies include the following:
- Listings of responsibilities for each member of the construction team (Owner, Architect, CM, GC, CxA, Subcontractors, Manufacturers, Independent testing Agencies, etc.)
- Require the CM/GC to run a building enclosure coordination preconstruction meeting attended by the Architect, third-party consultant, air barrier manufacturer, installer, and onsite representatives of trades that will interface with the air barrier material.
- State the requirements for stand-alone or in-place approved mock-ups to demonstrate acceptable installations of the air barrier that can be referenced throughout the project for comparison.
- State what testing of mock-ups and in-place work will be employed with clear references to industry standard test procedures and acceptance criteria.
4) Who is responsible for the air barrier submittals and shop drawings? Should the submittals and shop drawings be composed solely of manufacturer standard details?
The general contractor and sub-contractors are responsible for providing project specific shop drawings that include manufacturer input. All details relevant to the project should be provided including, but not limited to, intersections with other envelope assemblies, details showing how gaps in the construction will be bridged, inside and outside corner transitions, how claddings are secured with the air-tightness maintained, and how miscellaneous penetrations such as conduits, pipes, electric boxes and similar items are sealed. The shop drawings need to be reviewed and coordinated with related trades and reflect the sequencing of construction.
Manufacturer standard details can be used as shop drawings when they mimic the jobsite conditions. However, when the manufacturer standard details do not mimic the jobsite conditions, they are to be modified by the contractor with input by the manufacturer, to replicate project-specific conditions.
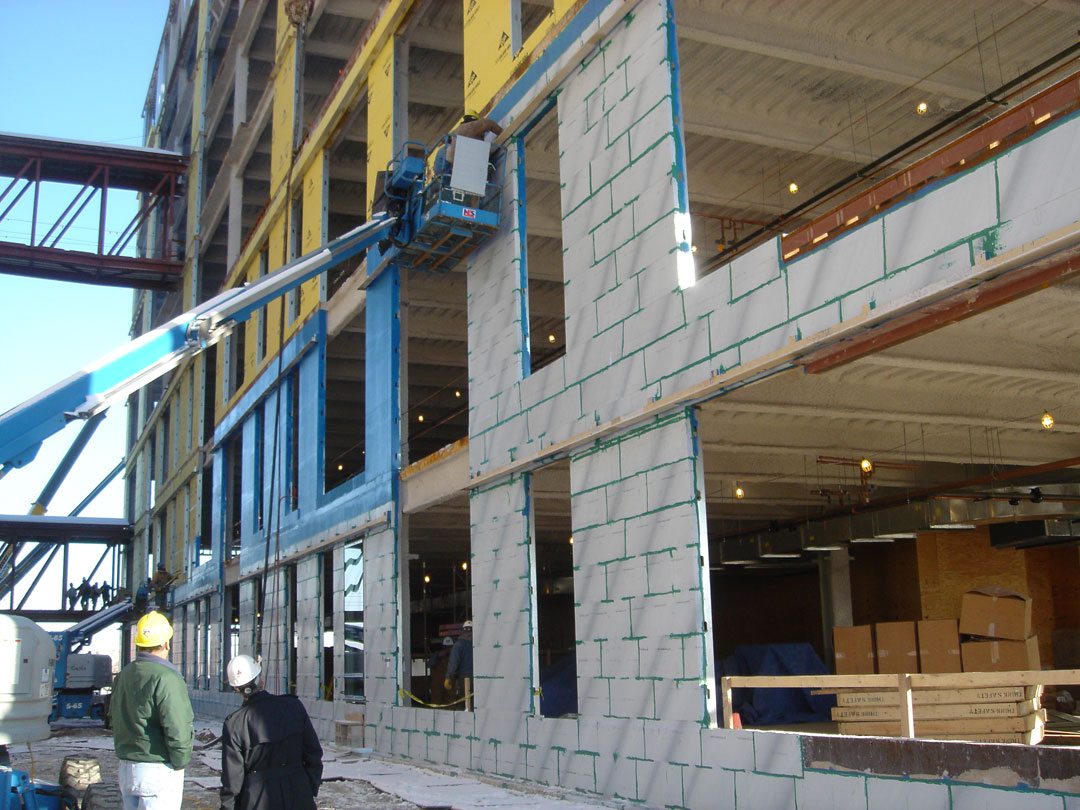
Children’s Hospital, Milwaukee Wisconsin. Credit: ABAA
5) Do pre-construction meetings for the air barrier have value? When should an air barrier pre-construction meeting be scheduled? What should the agenda be for the pre-construction meeting?
Yes, preconstruction meetings have value. They set the expectations for each participant and are an opportunity to raise questions and concerns. Having discussions up front, before the project is underway, is invaluable in heading off sequencing and compatibility issues that might otherwise become a later non-compliant issue.
The meeting should take place between 2-4 weeks prior to installation start-up.
The pre-construction meeting’s agenda should be outlined in the specification and include a discussion of the substrate acceptability, material installation limitations, communication of special project site considerations, discussion of installation sequencing and logistics, interface detailing review, discussion of constructability issues, response to questions provided by the subcontractors, and how non-compliant conditions can cause an interruption of the work ( and so should include a procedure for restarting the work after corrections have been made).
6) Why should site constructed mock-ups be required in project specifications?
It is necessary to establish that the assembly is a repeatable representation of the site specific work that meets the specified performance requirements, demonstrates material installation, and addresses work sequencing and workmanship.
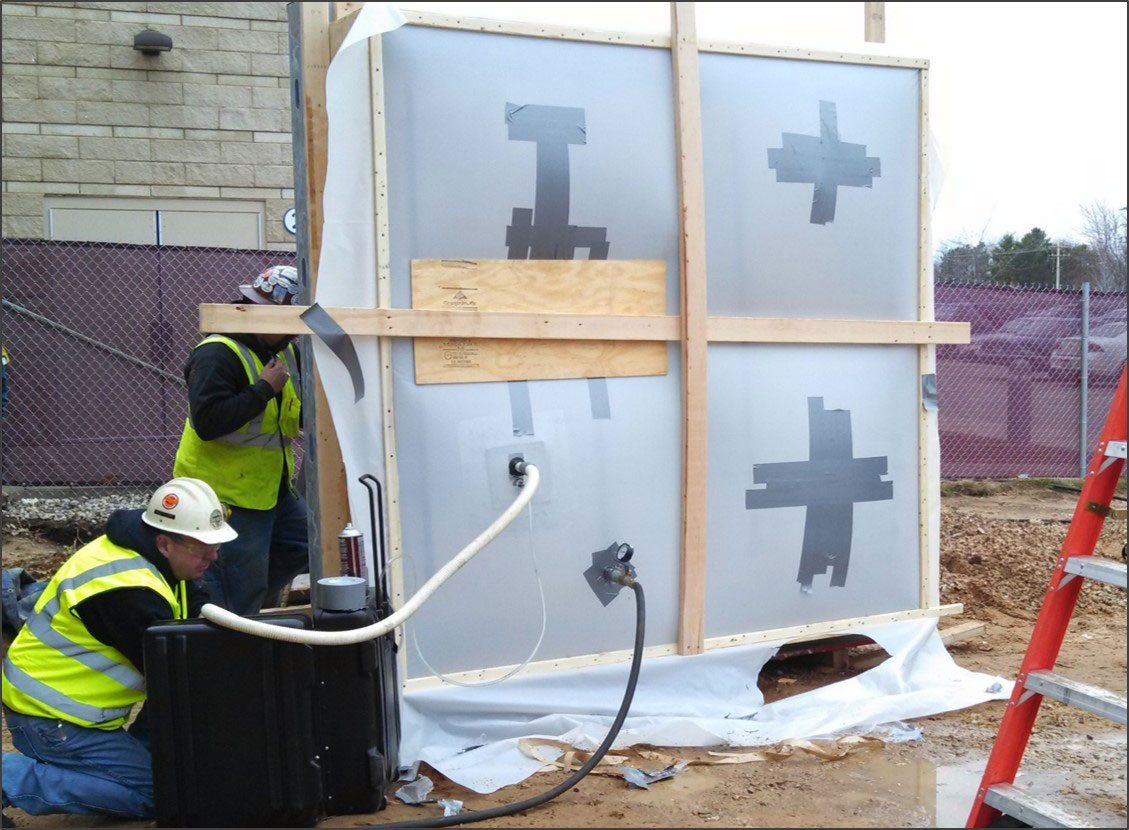
Mock-up testing. Credit: Boldt Construction
7) Who is responsible for the coordination necessary for the successful installation of the air barrier? How is coordination implemented?
The CM/GC is responsible for the air barrier installation coordination. Implement the coordination effort by stating in the Division 1 specifications that the CM/GC is required to provide a specific coordinator responsible for sequencing the air barrier/building enclosure interfaces that involve multiple subcontractors and manufacturers.
8) Who should be responsible for verifying the continuity of the air barrier installation and for field performance testing?
The specifications should state that the CM/GC shall be responsible for the QC/QA of the air barrier installation and for creating and implementing a strict documentation program which includes a reporting system to inspect and track non-conforming installations. Repairs to the air barrier should be conducted in accordance with manufacturer requirements and become part of the documentation.
9) Who is to provide the performance verification of the air barrier installation?
Pursuant to the performance verification provisions of the ABAA QAP, verification and documentation of the air barrier installation information rests with the Installer. Within that responsibility, the Installer is to provide daily site observations, and adhesion, thickness, and density testing, as applicable, of the installed product. Information from these daily activities is to be recorded in daily logs by the Installer and is to be accessible to all members of the team. The role of the ABAA auditor is to examine the Installer’s records, verify the installer testing and conformance to the manufacturer’s installation requirements, and perform independent testing.
The CM/GC is responsible to assure that the applicator follows the ABAA QAP, for coordination of trades and their work sequences, and protection of the installation.
If the ABAA QAP is not specified, the responsibility of verifying air barrier performance falls to the Designer who will specify performance criteria and testing standards, and who will conduct periodic site observations to verify that the air barrier installation is per manufacturer’s recommendations and project specifications. The Designer’s specification should note that the owner will contract with a third party entity for the independent inspection and testing.
10) Are through-wall flashings part of the air barrier system?
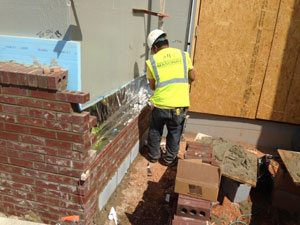
Through-wall flashings (TWFs) and air barriers. Credit: York Manufacturing
Through-wall flashings (TWFs) and air barriers are integral parts of a successful water management system. Where TWFs are required to interface with the air barrier to provide continuity of the water management system, they must also be integrated in such a way as to maintain continuity of the air barrier. Selection of appropriate flashing materials and their related installation sequencing is crucial to their successful integration with the air barrier holding continuity and chemical/adhesive compatibility in mind.
Editor’s note
All information in this article is from ABAA’s TECHNICAL BULLETIN ON AIR BARRIERS 1600 Boston-Providence Hwy, Walpole, MA 02081. Date of issue: 22-June-2016 D-115-015 rev 0 ABAA – Top 10 Frequently Asked Questions about Air Barriers
About ABAA
The Air Barrier Association of America (ABAA) is a national, not-for-profit trade association that consists of a wide cross section of stakeholders in the building enclosure industry. Their membership includes manufacturers, architects, engineers, trade contractors, researchers, testing & audit agencies, consultants and building owners. ABAA is the national voice of the air barrier industry and has raised the level of quality in the industry through a Quality Assurance Program and offers premier training, certification, product evaluations, contractor accreditation and site quality control audits. ABAA is active in the areas of research, education, standards development, building codes and technical resources for the air barrier industry.