The Mason Square Apartments II at Indian Motorcycle project offers low-income residents affordable rental housing without compromising aesthetics, performance or comfort. Part of a local area redevelopment program in Springfield, Massachusetts, the adaptive reuse and renovation project converted a former motorcycle factory into 45 apartments including one-, two- and three-bedroom units.
Vacant for decades, the 55,000-square-foot, five-story, brick building’s tall, arched windows had been boarded up for years. Today, these 4-by-8-foot openings feature Diamond Windows & Doors‘ high-performance, double-hung windows with Technoform‘s warm-edge insulating glass spacers. Beyond contributing to the building’s energy efficiency and the residents’ comfort, the windows were thoughtfully designed to match the property’s historic architecture.
Mason Square Apartments II is located in the McKnight National Historic District of Springfield at 837 State Street. The property also is listed on the U.S. National Park Service’s National Register of Historic Places.
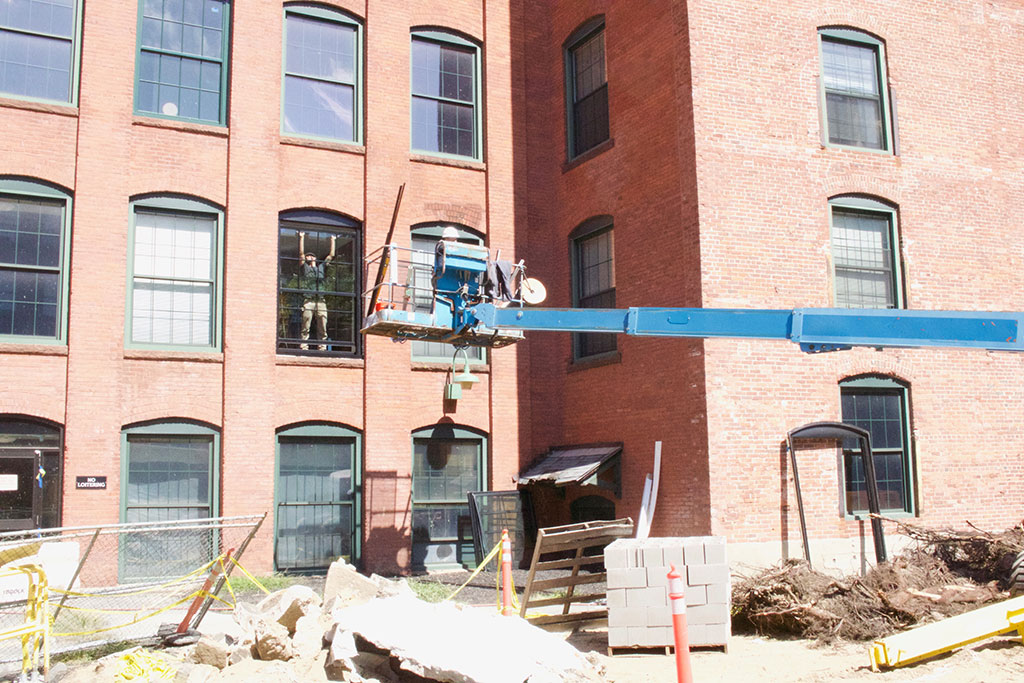
During project. Photo courtesy of Diamond Windows & Doors and Technoform
Originally built in 1890, the building is famously known as the Indian Motorcycle‘s former manufacturing mill facility. The company is credited with producing one of the first motorized bikes, and is considered to be the premier manufacturer of motorcycles in the racing industry. Their employees’ efforts, and the motorcycles they made, contributed to providing agile transportation to U.S. troops in World Wars I and II. The motorcycles were distributed nationwide until the 1950s, and in 2011, the brand was reintroduced.
Mason Square Apartments II’s owner and developer, First Resource Development Company, recognized the need to preserve the building’s architectural legacy. In addition, it celebrated the property’s significance to the community by incorporating “at Indian Motorcycle” as part of the official name.
“With every project we are mindful of neighborhood history; we are committed to building on the positives that each unique history conveys to a community,” said First Resource’s president Gordon Pulsifer. “We also look to the future, serving as a catalyst for improvement and change.”

Before photo of project. Photo courtesy of Diamond Windows & Doors and Technoform
To retain the building’s historic aesthetic and enhance its modern performance, First Resource worked closely with The Architectural Team and NEI General Contracting. Existing masonry was repaired, and the former factory’s massive interior timber beams were retained. The large window openings also were preserved, and approximately 1,300 new, high-performance, double-hung units from Boston-based Diamond Windows & Doors were installed.
“This was an historic project requiring the windows to pass muster with National Parks and Massachusetts State Historic Agencies,” explained Technoform’s Matt Fralick.
“Diamond was chosen due to our expertise in replicating the historic look and feel of the building and specifically, the windows,” said Erik Tseng, Diamond’s project manager. “We were also able to engineer the opening/window interface to reduce labor costs and provide a significant enhancement to energy performance and building envelope performance.”
Diamond Windows & Doors’ installed its 8000 Series Commercial double-hung windows. Technoform’s 1/4 inch-wide rigid bar, plastic hybrid stainless steel warm-edge spacers provided the important thermal break between the panes of glass in the insulating glass unit, to minimize unwanted heat loss.
Along with increased energy performance, the warm-edge spacer also improves condensation resistance. Fralick added, “Minimizing condensation lowers the opportunity for mold and mildew, which supports good air quality, health and wellness.”
Honoring the building’s architectural heritage, the aluminum frames were painted black to resemble old steel-framed factory windows from the early 20th century. Complementing the frame color and overall appearance, Technoform supplied its warm-edge thermal spacer in black. Fralick noted, “The dark spacer in the dual-glazed insulated glass units (IGUs) maintain the monolithic appearance of the original windows.”
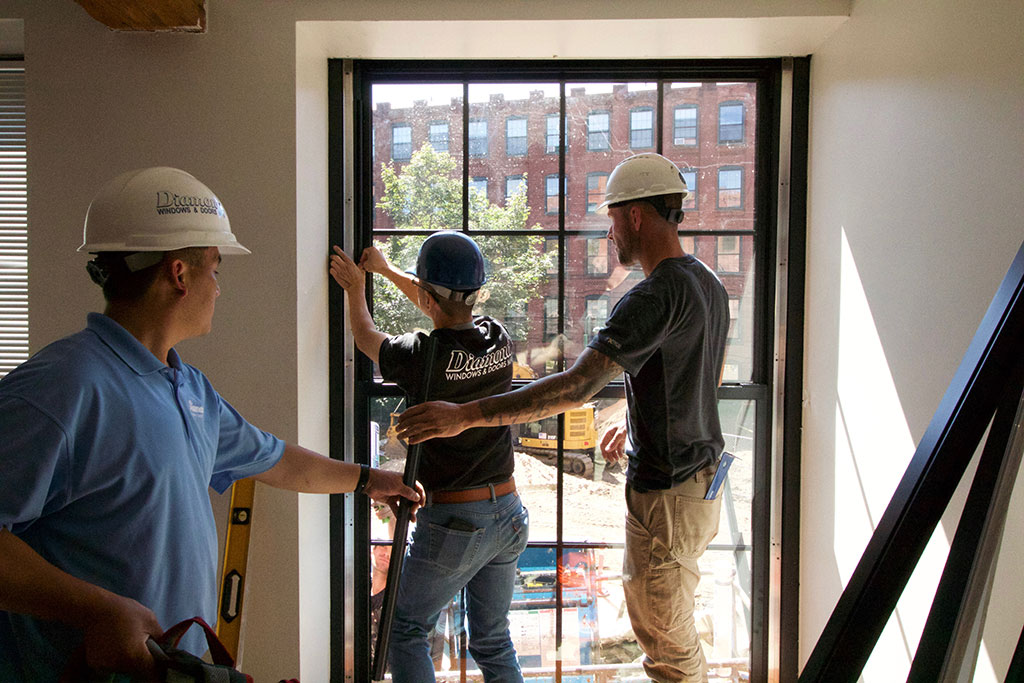
During project. Photo courtesy of Diamond Windows & Doors and Technoform
Further contributing to the windows’ thermal performance, the IGUs are fabricated with a clear Solarban® 60 solar control, low-e glass by Vitro Architectural Glass and argon gas fill. The high thermal performance of the new windows supports First Source’s energy efficiency goals, helping the building owner save on heating and cooling costs, as well as providing Mason Square’s residents with year-round interior comfort.
The total renovation and rehabilitation costs of Mason Square Apartment II was funded through a combination of public and private financing, institutional low-income housing tax credits, and federal and state historic preservation tax credits.
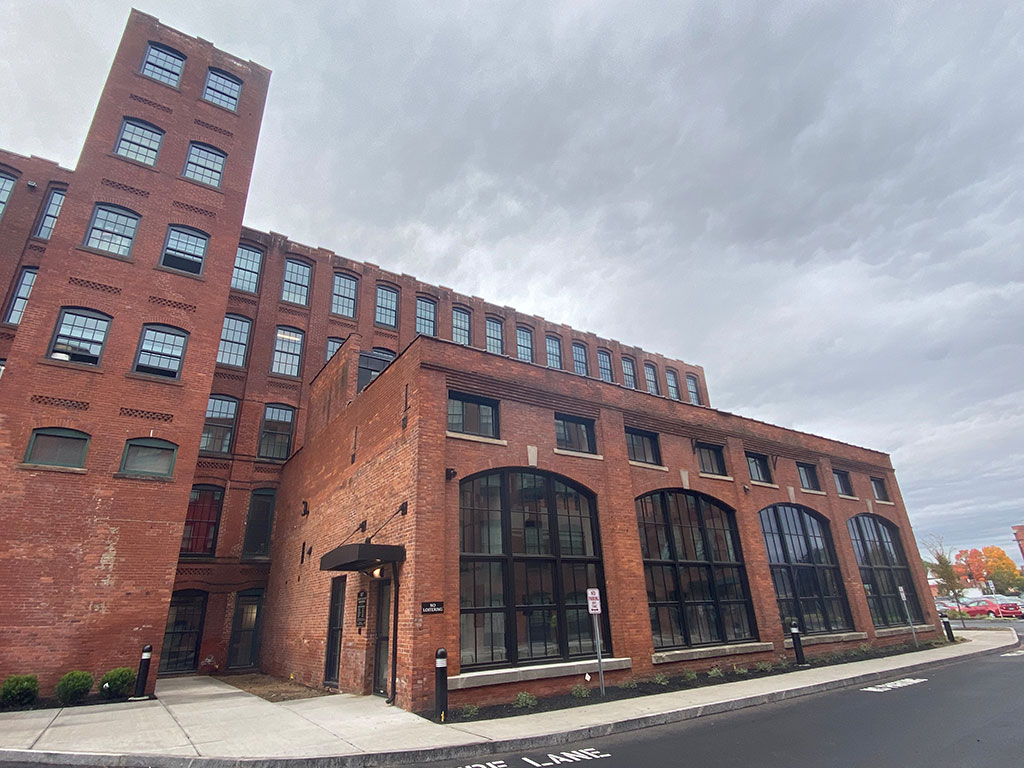
After photo of project. Photo courtesy of Diamond Windows & Doors and Technoform
At a groundbreaking celebration in June 2019, MassLive.com reported that local officials including Mayor Domenic J. Sarno and state Rep. Bud L. Williams, praised First Resource and Pulsifer for bringing new life to the area. Williams called it an historical day and expressed his hope that the project will serve as a catalyst for other developments in the surrounding area.
In addition to Mason Square Apartments II, First Resource also owns the adjacent former fire station and neighboring factory building. These also are being converted into affordable and market-rate residential rental units.
Mason Square Apartments II at Indian Motorcycle, 837 State St., Springfield, MA 01109 http://www.firstresourcecompanies.com/l/mason-square-apts-ii-at-indian-motorcycle
• Owner/developer: First Resource Development Company; Hanover, Massachusetts; http://www.firstresourcecompanies.com
• Architect: The Architectural Team, Inc. (TAT); Chelsea, Massachusetts; https://www.architecturalteam.com
• General contractor: NEI General Contracting, Inc.; Randolph, Massachusetts; https://www.neigc.com
• Glazing contractor: Hannah Environmental & Energy, Inc.; Londonderry, New Hampshire
• Replacement window system – window and insulating glass fabricator: Diamond Windows & Doors MFG Inc.; Boston; https://www.diamondwindows.com
• Replacement window system – coated glass: Vitro Architectural Glass; Cheswick, Pennsylvania; https://www.vitroglazings.com
• Replacement window system – insulating glass spacer: Technoform; Twinsburg, Ohio; https://www.technoform.com
• Photography: courtesy of Diamond Windows & Doors
Technoform provides high-performance insulative solutions for façades, cladding and fenestration systems. Its best-in-class building envelope products are developed through collaboration with its customer partnerships to boost thermal performance of windows, curtainwall and opaque façades. The relative low cost and high performance of Technoform’s components help building designs to balance energy efficiency with occupant health and comfort without compromising aesthetics.
For more information on Technoform’s insulating solutions for façade, cladding and fenestration systems in North America, please email info.us@technoform.com, call 330-487-6600 or visit www.technoform.com.