An airtight building enclosure is an important part of a modern building. Good airtightness can increase energy efficiency, improve durability, and allow greater control over occupant comfort and indoor air quality. Airtightness is achieved with an effective air barrier system that is carefully designed and detailed and then built and commissioned in the field. An effective air barrier consists of a continuous system of materials (building wraps, membranes, etc.), components (doors, windows, etc.) and accessories (tapes, sealants, gaskets, etc.). These air barrier elements must be individually airtight and airtight when used together.

Air Barrier Systems consist of many components, materials, and accessories sealed as part of the building enclosure. Image Credit: RDH Building Science
Airtightness requirements in building codes and energy performance standards are becoming increasingly stringent across North America. Historically, many codes and standards have included only requirements for the air permeance of materials and components in building enclosure assemblies. The expectation was that if airtight materials were used to construct the building enclosure then the end result would be airtight. However, experience has shown that the majority of air leaks occur at joints and interfaces between these air barrier elements, and as a result the requirements for how airtightness is specified and measured have shifted. More recent codes and standards have now begun to also include targets for whole-building airtightness as a way of achieving consistently higher levels of performance. To achieve these targets, airtightness must be considered through all phases of a building project, from design through construction to completion. To confirm these targets have been met, airtightness testing is done to measure the performance of the complete and installed air barrier system.
Many people may be familiar with airtightness testing for small buildings including houses where a single “fan-door” or “blower-door” piece of equipment is used to pressurize and depressurize the space. This type of testing has become commonplace across Canada and the US for weatherization or energy retrofit work in existing homes and for commissioning of air barrier systems in new construction. Large building testing follows the same concept but is performed at a larger scale in terms of the necessary teamwork involved and often requires the use of more than one high-powered fan door to perform a whole-building test.
Increasingly stringent airtightness targets have broadened the discussion surrounding air barrier elements beyond material airtightness. Materials and components should be considered in the context of the system they are part of and not in isolation. Considerations include the specific air barrier details, material compatibility, and long-term durability. Given the wide range of materials and details, there has also been an increasing awareness of the benefit of robust quality control and assurance protocols to verify the compatibility of materials and substrates, as well as the practical challenges faced during construction.
In jurisdictions where large building airtightness testing is mandated, including Washington State, ongoing test results are valuable insights into the design and construction of air barrier systems. There have been shifts in the local construction market with preferences to higher-performance air barrier systems and increasing reliance on manufacturers to provide compatible air barrier material solutions from enclosure components from the roof to below grade. There has also been a shift in the design and selection of appropriate air barrier strategies for taller buildings which are more robust and able to accommodate the higher air pressures caused by wind, stack effect, and mechanical systems in taller buildings.
How Do Current Buildings Stack Up
While current energy performance and airtightness standards set the requirements for overall building airtightness, it is useful to compare against the results of previous whole-building airtightness: this data provides context for what airtightness levels are expected and achievable in larger buildings as they have different air barrier approaches and considerations from houses. Historical data can be easily compared and analyzed using the Normalized Air Leakage Rate metric. In a recent study of whole-building airtightness testing[1], the results of several hundred large building airtightness tests from Canada, the United States, and the United Kingdom were compiled and analyzed.
The chart below shows the distribution of the results of this study for buildings tested in Seattle, where airtightness testing is mandatory. For comparison, the chart shows a relative indicator of the levels of airtightness found in each test, rated as exceptional, good, moderate, and poor airtightness. Testing showed that most buildings met the minimum airtightness requirements, with many far exceeding them and achieving excellent results.
In the same study, newer large buildings in jurisdictions with mandatory airtightness requirements (United States Army Corps of Engineers (USACE) and Washington State) were compared with those with no airtightness testing requirements. As shown in the chart below, the results indicate that buildings that are built with the intent of meeting a minimum airtightness requirement can consistently achieve and even exceed the minimum target, while new buildings built with no minimum airtightness requirements are generally less airtight. For buildings required to meet the USACE and the Washington state requirements, the majority are well below the minimum airtightness requirements, with only a few outliers. The takeaway from this study is that high levels of airtightness can be achieved if the motivation is there – good strategies are available.
Effective Air Barrier System Strategies for Exterior Walls
The design of an effective air barrier system requires selecting materials, components, and accessories that can be combined to control air leakage. While relatively straightforward to achieve in the field of an assembly, ensuring continuity of the air barrier at interfaces and penetrations of the building enclosure is critical to air barrier performance. An effective air barrier should have the following attributes: air impermeability, continuity, durability, strength, and rigidity appropriate to the building type and expected service loads.
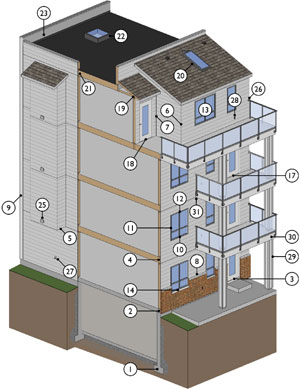
The many details and air barrier system details required as part of a typical larger building. Image credit RDH
Appropriate exterior wall air barrier systems and details are often the primary focus of design for architects and engineers as they tend to be the most complex and detailed systems, though that doesn’t mean that the roof, below grade, and interface systems and details are any less leaky or unimportant. Roof air barrier systems for low-slope roofs consist of either the roof membrane or a supplemental air/vapor barrier membrane, and below grade waterproofing systems consist of applied liquid or sheet-applied products. Joints and interfaces are typically sealed with membranes and sealants. With exterior walls there are more choices, and different systems have different detailing and construction implications so are worth a further discussion here.
Wall air barrier systems can generally be grouped into two conventional types: exterior air barrier systems, with the primary airtight elements placed at the exterior side of the enclosure, and interior air barrier systems, with the primary airtight elements installed at the interior side of the enclosure. Within these systems there are various approaches and components used to achieve the air barrier.
The exterior air barrier approaches use an airtight layer, usually a dedicated membrane, installed over the exterior face of the building, and made continuous with tapes, membranes and sealants over joints, transitions and penetrations. The interior approaches use an airtight layer applied from the interior of the enclosure, interfacing with the various interior elements, transitions, and penetrations. In general, the exterior approach is a simpler and favored method for larger and taller buildings, since it does not interface with numerous interior elements like framing or service penetrations for electrical and plumbing. In addition, because the components of the exterior air barrier are often also used as the water-resistive barrier (for example a synthetic house wrap on walls), the effort and care required to achieve a continuous layer to resist moisture intrusion also contributes to the overall continuity of the air barrier.
For exterior air barrier systems there are three primary generic approaches used on larger and taller buildings: the sheathing membrane approach, the sealed sheathing approach, and the liquid-applied membrane approach. Other proprietary materials and systems can also be grouped into these classifications in terms of how they are sealed. Whole building airtightness testing data of large buildings incorporating these three primary exterior air barrier approaches has shown that all three can meet current code requirements (often between 0.25 and 0.40 cfm of air leakage per square foot of enclosure area at a test pressure of 75 Pa)[1]. Testing has also shown that the more rigid and adhered sheet- or liquid-applied membrane approaches tend to be more reliably air tight and easier to maintain during construction, especially for taller and more exposed buildings. There are obvious material and labor cost differences between the various approaches which should be factored in as well.
The selection of materials and detailing of exterior air barrier systems must include considerations for durability both during construction and in service, material compatibility to adjoining materials, adhesion to substrates and adhesion of product to itself, and constructability. It is also important to consider the expected weather and the ability to adequately prepare the substrate to manufacturer requirements for each of the air barrier materials being used.
Sheathing Membrane Approach – Mechanically Attached and Self-Adhered
Mechanically fastened systems use an airtight sheathing membrane, attached to the exterior sheathing with fasteners and washers. Joints, penetrations, and laps are made airtight using sealant, tape, and self-adhered sheathing membrane strips as needed. This is a commonly used exterior air barrier system for low-rise wood frame construction. Care should be taken to ensure the sheathing membrane is adequately attached to the building during construction and it should be supported by strapping or cladding to avoid damage. This approach is not typically appropriate for taller buildings or those with higher design wind loads due to the pressures applied on the mechanical fasteners, tapes, and sheet interfaces.
Self-adhered sheathing membranes rely on adhesion to both the substrate and at membrane laps in order to be airtight. The membrane should also be installed onto a suitable substrate such as wood sheathing, gypsum sheathing, concrete, or concrete block that is dry and provides continuous backing. Self-adhered membranes essentially make the membrane and backup material part of the air-barrier system from a structural load and continuity standpoint. Compared to mechanically attached sheets which are spot fastened to the substrate, self-adhered membranes restrict lateral air movement behind the membrane, which helps with overall system airtightness, especially around details. Self-adhered membranes also easily span over joints and gaps within the substrate unlike liquids which require special joint treatments and/or reinforcing.
Sealed Sheathing Approach
The exterior sheathing, when sealed at joints and interfaces, can also act as the primary air barrier element. This approach uses the exterior sheathing together with either sealant, liquid-applied sheathing membrane, strips of membrane, or sheathing tape to create a continuous air barrier at the sheathing joints. A sheathing membrane is often required with this approach to provide the water-resistive barrier. Within the past few years a number of proprietary coated sheathing products that function as both air- and water-resistive barrier systems have been developed following this approach.
Liquid-applied Membrane
Exterior liquid-applied membranes share many of the advantages of self-adhered membranes and are especially useful for complex detailing. Liquid-applied membranes rely upon a supporting substrate to provide a continuous backing in order to achieve an airtight barrier. Joints typically require specific detailing considerations and often incorporate membrane reinforcement. The substrate and weather conditions can have a significant impact on curing time and adhesion. The manufacturer’s instructions should be strictly followed. Liquid-applied membranes are generally used as the water-resistive barrier, and must be installed and detailed as such.
Testing for Closure
Large building airtightness testing is quickly becoming commonplace in many jurisdictions across North America as a result of new building code requirements or as part of enhanced commissioning programs. Testing of large buildings thus far has found that it can be relatively straightforward to meet current airtightness targets when starting with good design and planning, appropriate materials and air barrier strategies, proper site implementation, and quality control, all of which is verified by commissioning testing. There are literally hundreds of options and materials that can be used to form part of the air barrier system and the appropriateness of different products and systems depends on the type and exposure of the building along with the expected loads during construction and in service. Fortunately, with commissioning testing becoming more commonplace, people are very quickly figuring out the better approaches and buildings are becoming more air tight, which is good for more efficient, durable, and comfortable buildings.
[1] http://rdh.com/wp-content/uploads/2016/06/Whole-Building-Airtightness-Testing-and-Results-Report.pdf
Click here for details on the above-grade membranes available from Dorken.
About the author
Graham Finch, Dipl.T., M.A.Sc., P.Eng.
Principal, Building Science Research Specialist
Graham Finch is a building science engineer who specializes in research and investigation work and leads RDH’s research group. His work experience includes a wide range of projects including building enclosure condition assessments, forensic investigations, research studies, energy assessments, building monitoring programs, field review, and testing services for new and existing buildings across North America. He has also worked with numerous building product manufacturers on product research and development, performance monitoring, and field testing.
Graham has authored several publications and practical industry guideline documents related to durable and energy efficient building enclosures, several of which can be found on the RDH website. Graham is also a part-time instructor at the British Columbia Institute of Technology where he teaches building science courses at the Diploma and Masters levels.
Graham is regularly invited by various building industry organizations and clients in Canada and the US to speak to the practical and technical issues of various building science topics. He actively publishes technical papers and presentations on building science research at local to international conferences.
Editor’s note
“Large Building Airtightness Testing and the Selection of Appropriate Air Barrier Strategies” by Graham Finch was originally published October 6, 2017 on the “Air & Moisture Control Blog“ published by Dörken. The “Air & Moisture Control Blog” is focused on delivering content that truly matters to the building industry. By making scientific evidence and global expertise available to everyone, from building professionals to home owners, we aim to change the way you see air and moisture barriers and the critical role they play in creating high-performance buildings. As part of this blog, you can expect to see commentary, expertise and insights from some of the industry’s leading experts in their fields.